Indice dei contenuti
Autori
- Francesco Palloni (SmartCAE),
- Stefano Milani (Ener Consulting)
Durante la verifica strutturale di un recipiente in pressione, capita spesso che l’approccio Design-by-Analysis basato sulla categorizzazione delle sollecitazioni porti ad un sovradimensionamento del componente. Ciò è legato al fatto che la procedura in questione è conservativa, pertanto tende a sovradimensionare i componenti sotto analisi.
Inoltre, dobbiamo tenere conto del fatto che la procedura di linearizzazione risulta particolarmente articolata ed onerosa se applicata su geometrie complesse.
In questi casi, le principali normative sui recipienti in pressione, prevedono la possibilità di applicare una tipologia di analisi più accurata, attraverso l’esecuzione di calcoli non lineari.
Cosa intende la normativa ASME per Analisi Non Lineare?
La normativa ASME, permette la verifica dei recipienti in pressione utilizzando una legge costitutiva non-lineare. Questo tipo di modello costitutivo, che permette la modellazione dello snervamento e della conseguente plasticizzazione, tipica degli acciai e delle leghe duttili in genere, da una parte costringe l’analista a introdurre nel modello matematico una legge costitutiva più complessa, da un’altra richiede che il solutore permetta questo tipo di analisi.
Vantaggi dell’approccio Non Lineare
Come abbiamo già accennato prima, l’approccio non lineare offre un range di ammissibilità maggiore. Questo comporta che, a parità di geometria e materiali, il componente è in grado di offrire prestazioni superiori rispetto a quelle ottenibili con una verifica lineare elastica.
Un secondo vantaggio, è dato da una fase di post-processing che risulta più immediata, come vedremo fra breve.
Svantaggi dell’approccio Non Lineare
D’altro canto, l’analisi non lineare presenta una serie di svantaggi rispetto alla procedura di categorizzazione delle sollecitazioni.
I tempi di calcolo di una analisi non-lineare sono superiori a quelli di una analisi statica lineare, a parità di mesh e condizioni al contorno.
La fase di preparazione del modello matematico risulta più complessa, in quanto è necessario ricavare la legge costitutiva del materiale.
L’approccio non-lineare porta a margini di sicurezza inferiori, pertanto si deve prestare maggiore attenzione all’impostazione della verifica (carichi di progetto, condizioni al contorno, mesh ad elementi finiti, dati del materiale, …) per non incorrere in errori di valutazione.
Dobbiamo infatti considerare sempre che eventuali errori commessi dall’analista nella definizione matematica dell’analisi, nel caso della procedura di linearizzazione tendono, entro certi limiti, ad esser compensati, mentre nel caso di un analisi elasto-plastica, avendo margini di sicurezza ridotti, tali errori possono portare a criticità strutturali.
Un esempio di calcolo
Per confrontare la procedura di categorizzazione delle sollecitazioni con l’analisi non-lineare, facciamo riferimento a un caso di studio nel quale applichiamo entrambi i criteri di verifica. Il caso di studio è un serbatoio a fondo piano con spessore variabile, illustrato in Figura 1, mentre in Figura 2 sono riportare le condizioni di progetto.
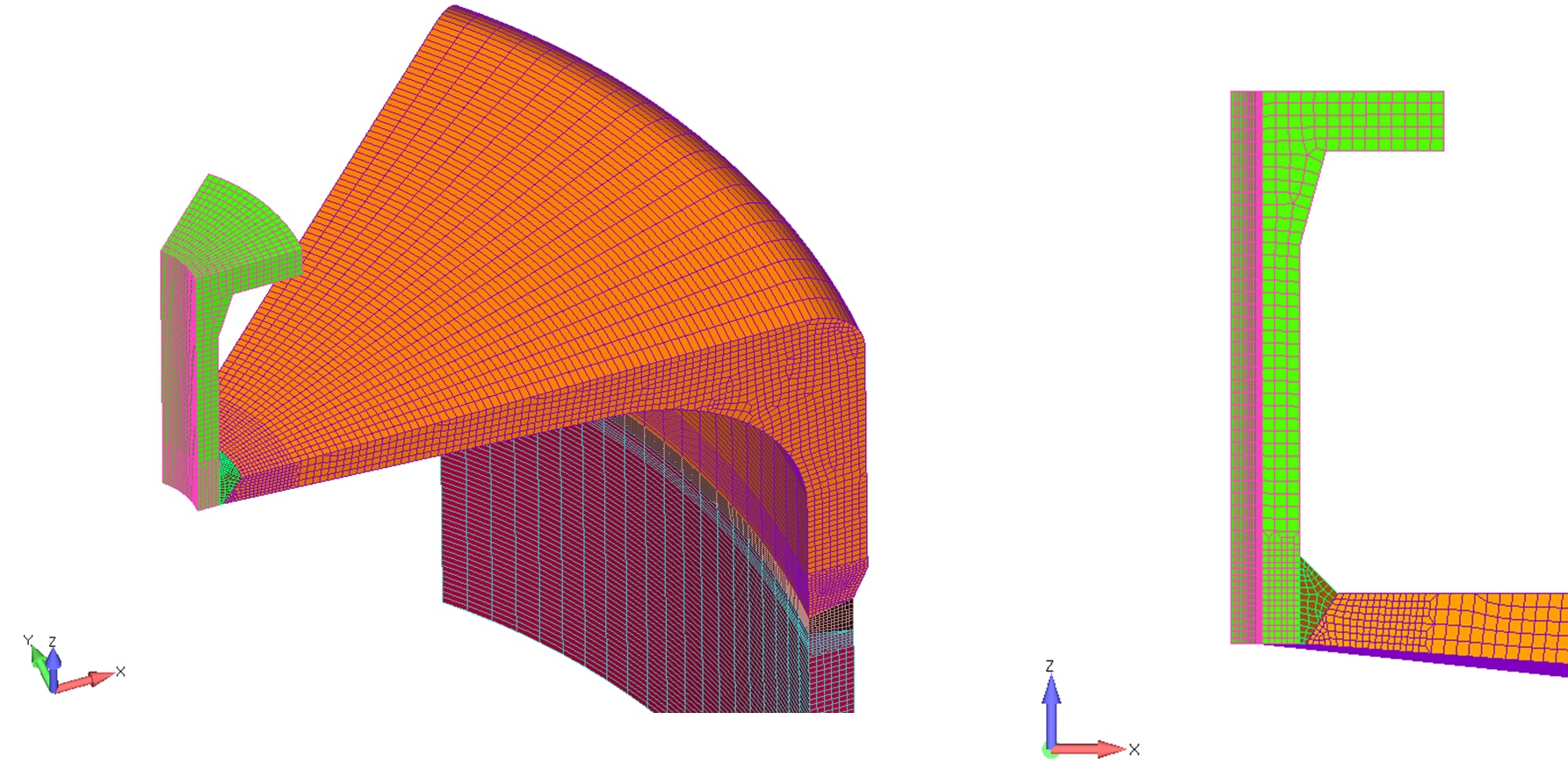
Figura 1 – Caso di esempio
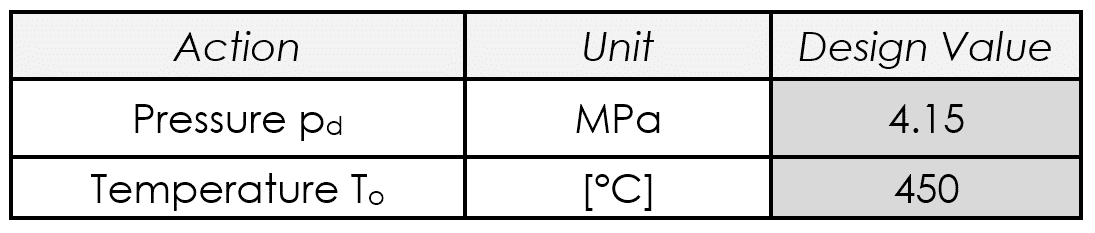
Figura 2 – Dati di progetto
Una prima osservazione in merito alla procedura non lineare è che in questo caso si devono necessariamente modellare tutti i dettagli (es. cordoni di saldatura). A tal proposito si è provveduto a ridurre la dimensione degli elementi in corrispondenza della saldatura tra fondo e bocchello, al fine di ottenere una migliore approssimazione dello stato tensionale-deformativo.
La Figura 3 illustra la verifica del cordone di saldatura in corrispondenza della giunzione tra fondo e bocchello attraverso la procedura di linearizzazione.
La sollecitazione Membranale è categorizzabile come Locale, mentre quella Flessionale risulta di tipo secondario.
Ciò nonostante, la componente membranale supera comunque i valori massimi definiti dalla normativa e, pertanto, il componente non risulta verificato, come indicato nella Figura 4.
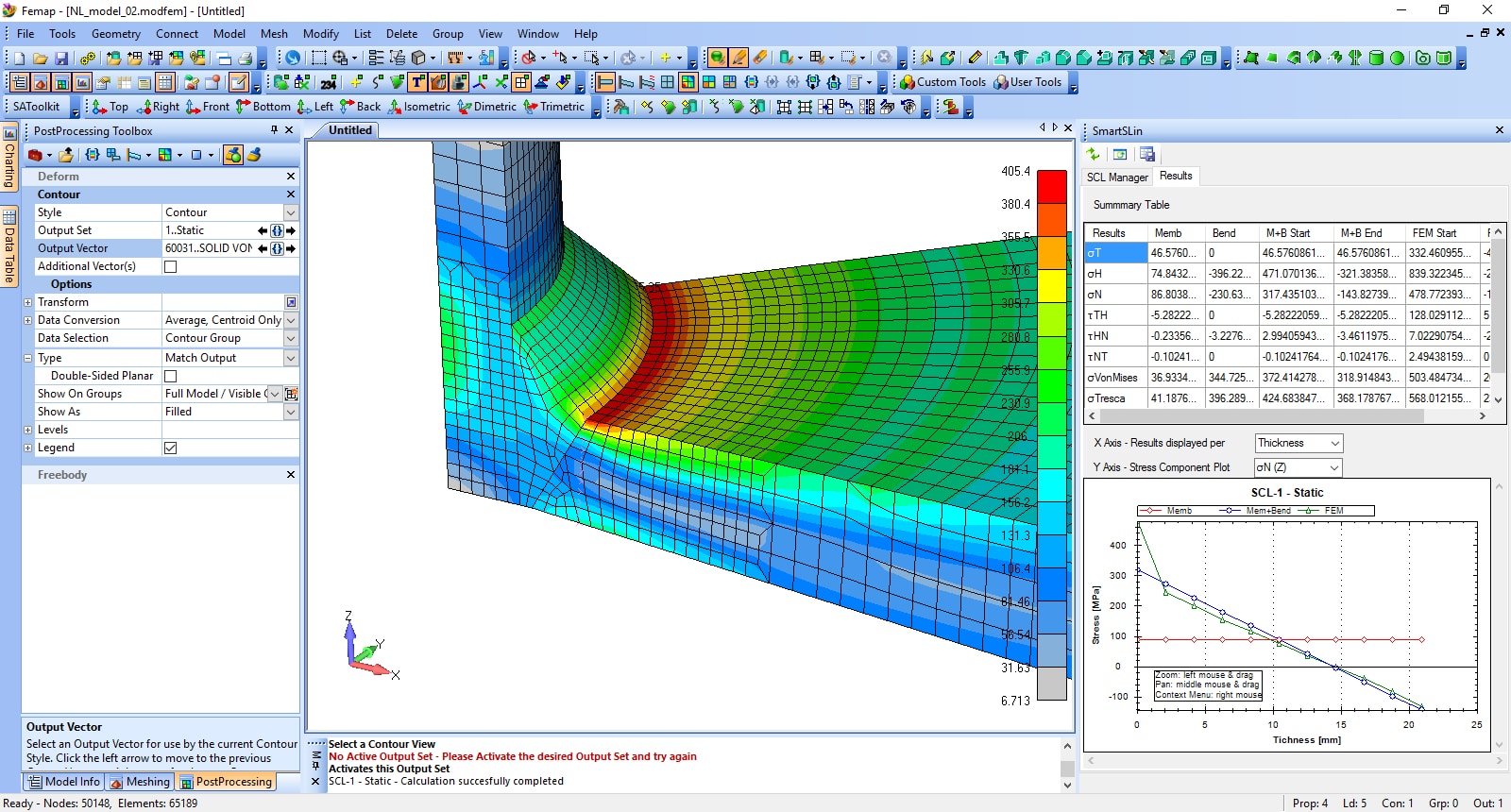
Figura 3 – Linearizzazione delle Sollecitazioni con Femap e SCL-Analyzer

Figura 4 – Verifica mediante Linearizzazione
Limit Load Analysis vs. Elastic Plastic Analysis
Facciamo un breve confronto tra le due procedure non lineari a cui fa riferimento la normativa ASME: Limit Load Analysis (Figura 5) e Elastic-Plastic Analysis (Figura 6). La procedura “Direct Route” della EN 13445-3 è concettualmente simile a queste. Dobbiamo infatti considerare che, sia nella normativa EN che in quella ASME, i carichi di progetto vengono maggiorati mediante un opportuno coefficiente dipendente dalla sua natura (meccanico, termico, ambientale ecc…).
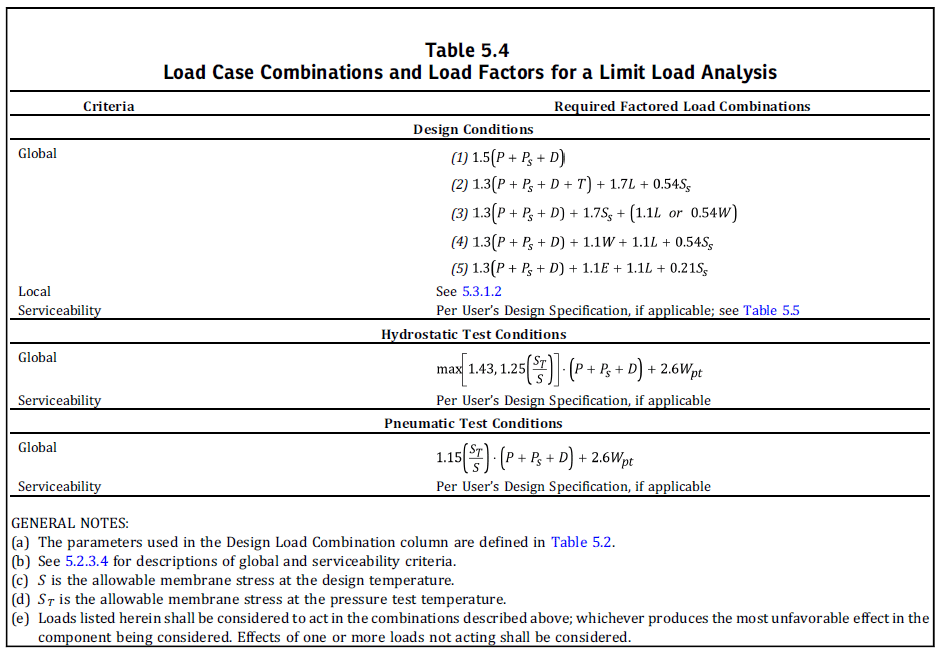
Figura 5 – Limit Analysis – Load Combination
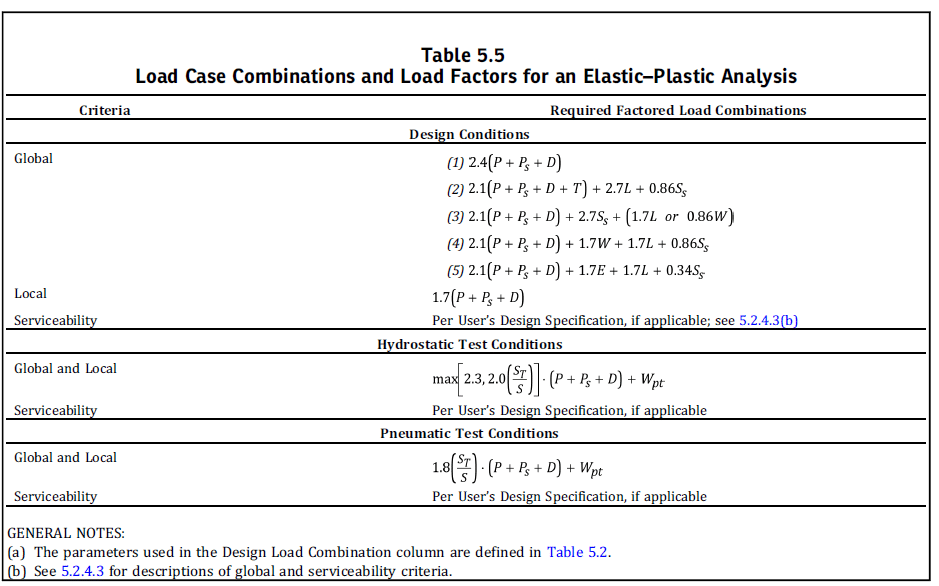
Figura 6 – Elastic-Plastic Analysis – Load Combination
Si tenga sempre presente che, per eseguire una analisi dei rischi completa, si devono valutare necessariamente tutti i fenomeni che possono portare al collasso strutturale del componente (Fatica, creep, buckling ecc…) purché questi siano applicabili.
Procedura Limit Load
Con la procedura Limit Load Analysis si può eseguire la verifica a collasso plastico globale, il materiale viene modellato come elastico-perfettamente plastico, trascurando pertanto l’incrudimento. Inoltre si fa riferimento alla meccanica dei corpi poco deformabili: questo è uno dei punti che differenzia la procedura limit load a quella elasto-plastica.
Procedura Elasto-Plastica
Nella procedura elasto-plastica si possono eseguire verifiche a collasso plastico globale e locale. La legge costitutiva tiene conto dell’incrudimento, ed in questo caso si passa dalla curva stress-strain ingegneristica a stress-strain vera. La normativa fornisce la procedura per determinare le legge costitutiva del materiale, in funzione della sua tipologia (acciaio al carbonio, basso legato ecc) e delle caratteristiche meccaniche di resistenza (snervamento e rottura). In questo caso, visto che stiamo facendo riferimento ad una legge costitutiva che tiene conto dell’incrudimento, i coefficienti di amplificazione dei carichi sono maggiori rispetto al caso precedente.
Legge costitutiva Non-Lineare
In Figura 7 è riportato l’andamento delle due leggi costitutive previste dai due diversi approcci non-lineari. In Figura 8 sono riportate le caratteristiche del materiale alla temperatura di progetto. Il valore dello snervamento da utilizzare per il calcolo deve essere ricavato mediante la relazione Sy=1.5S, indipendentemente dal valore tabellato nella normativa ASME II part.D.
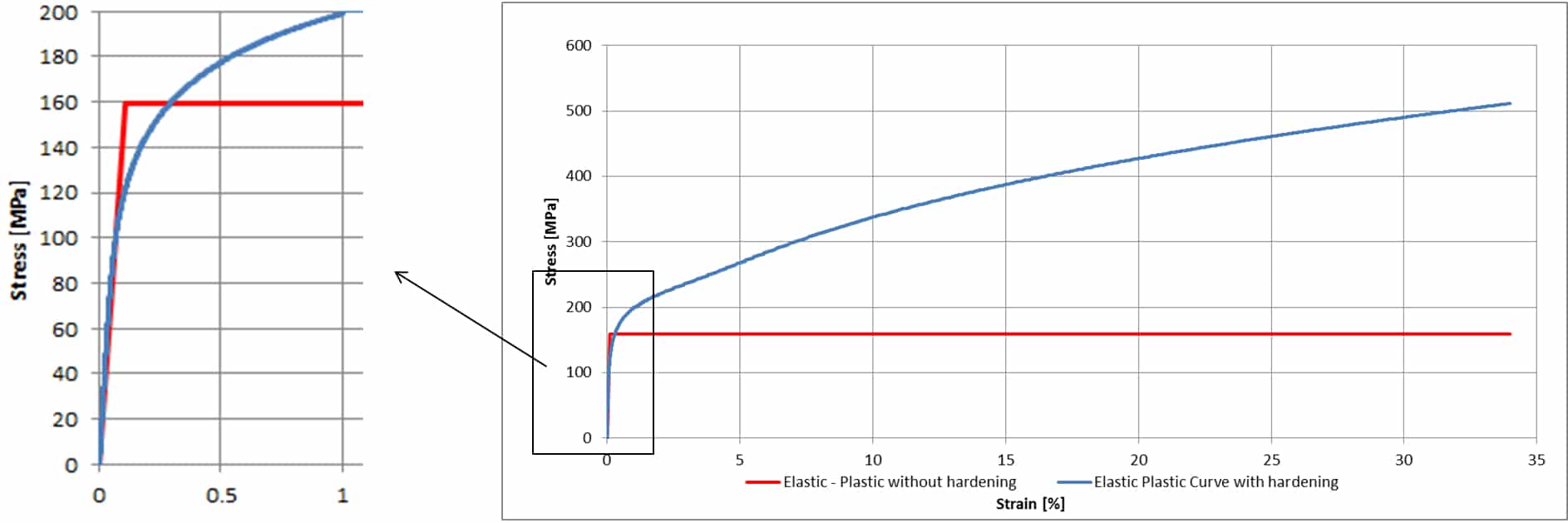
Figura 7 – Curve di Materiale Non Lineare
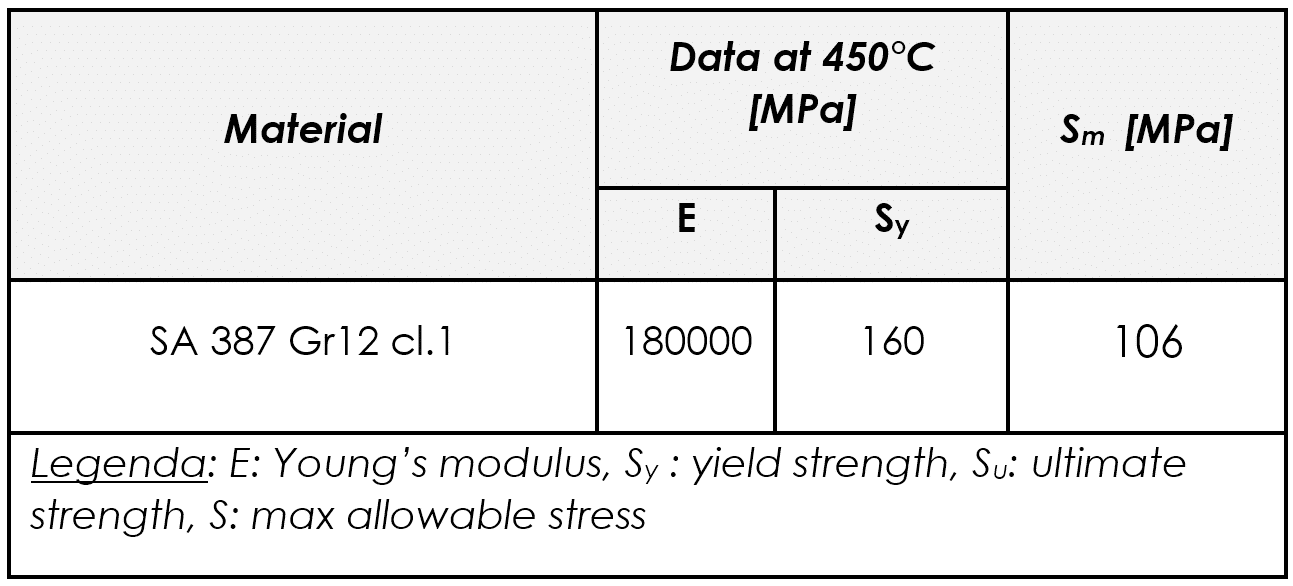
Figura 8 – Caratteristiche meccaniche del materiale
Nel caso in questione la differenza tra il valore di snervamento tabellato e quello calcolato dalla precedente formula è minima (1 MPa). Vi sono tuttavia materiali in cui questa differenza diventa più marcata, soprattutto se operanti ad elevate temperature.
La curva in rosso riporta l’andamento della legge elasto-plastica non incrudente prevista dalla Limit Load Analysis, mentre con la curva in blu viene mostrato l’andamento della legge costitutiva tensione-deformazione ricavata secondo ASME per la verifica Elasto-Plastica.
Collasso Plastico Globale e Locale
Con la verifica a collasso plastico globale si valutano eventuali cedimenti macroscopici del componente, infatti è sufficiente che l’analisi raggiunga la convergenza per poter considerare la verifica superata. Non andiamo pertanto a valutare alcuna grandezza tensionale o deformativa. Quando il solutore FEM raggiunge la convergenza vuol dire che il sistema ha raggiunto una configurazione di equilibrio tra le forze interne (tensioni) e le forze esterne (carichi). Questa verifica è possibile sia con l’approccio Limit Load che con quello Elasto-Plastica.
In Figura 9 sono mostrate le deformate della struttura utilizzando i due approcci: a sinistra è illustrato l’approccio “Limit Load”, a destra quello “Elastic-Plastic”. A causa dei diversi fattori di amplificazione dei carichi e la diversa curva del materiale, le deformate risultano diverse. In entrambi i casi il sistema raggiunge una configurazione di equilibrio, pertanto la struttura risulta verificata al collasso plastico Globale.
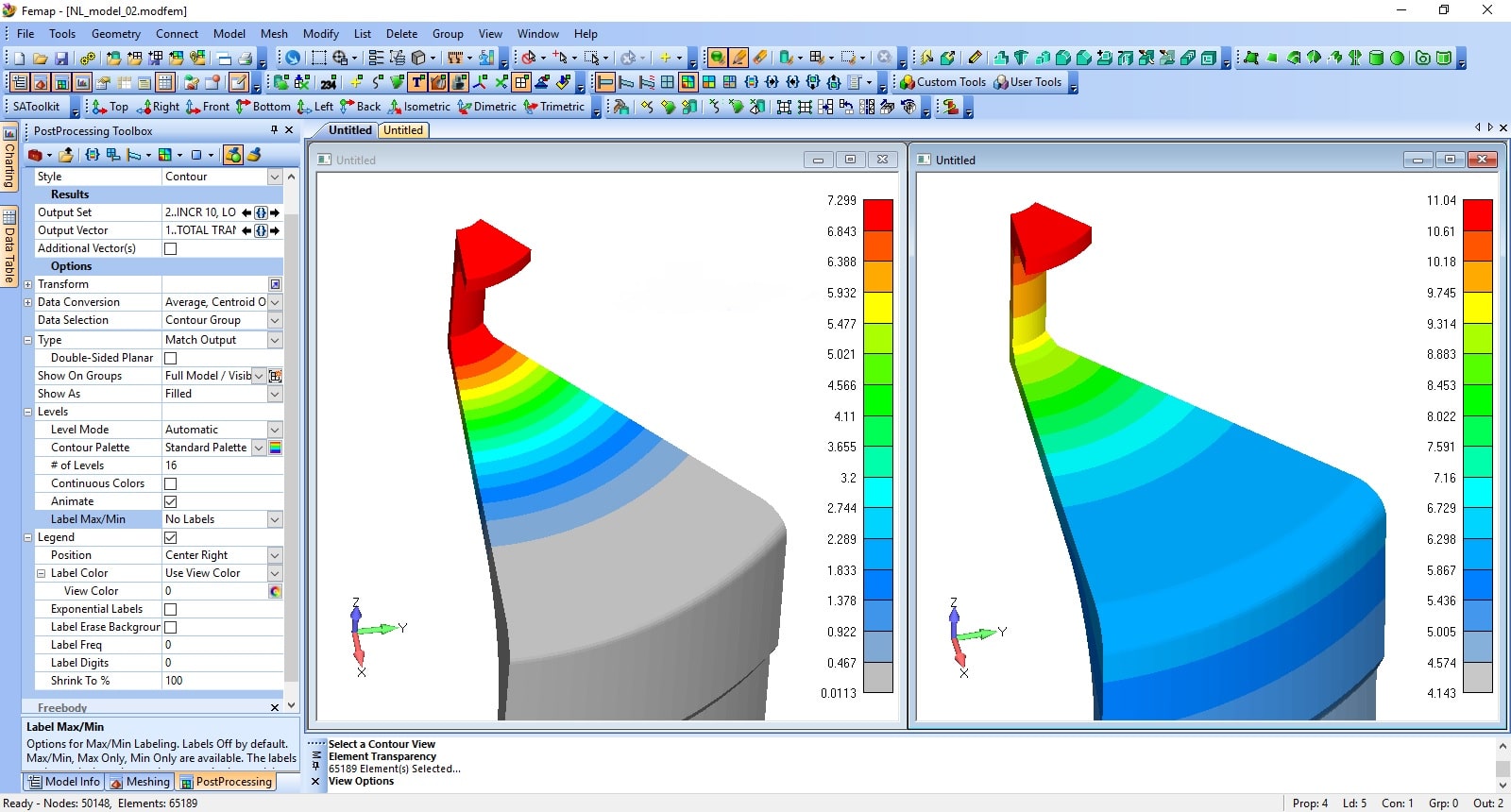
Figura 9 – Deformazione Limit Load e Elasto-Plastic
Collasso plastico locale
Con la verifica a collasso plastico locale andiamo a controllare che, nelle zone critiche del nostro componente, non vengano a generarsi deformazioni che possano portare a criticità strutturali. Questa verifica è possibile soltanto con l’analisi Elasto-Plastica.
Figura 10 mostra l’andamento delle deformazioni equivalenti elasto-plastiche nella zona di massima critica.
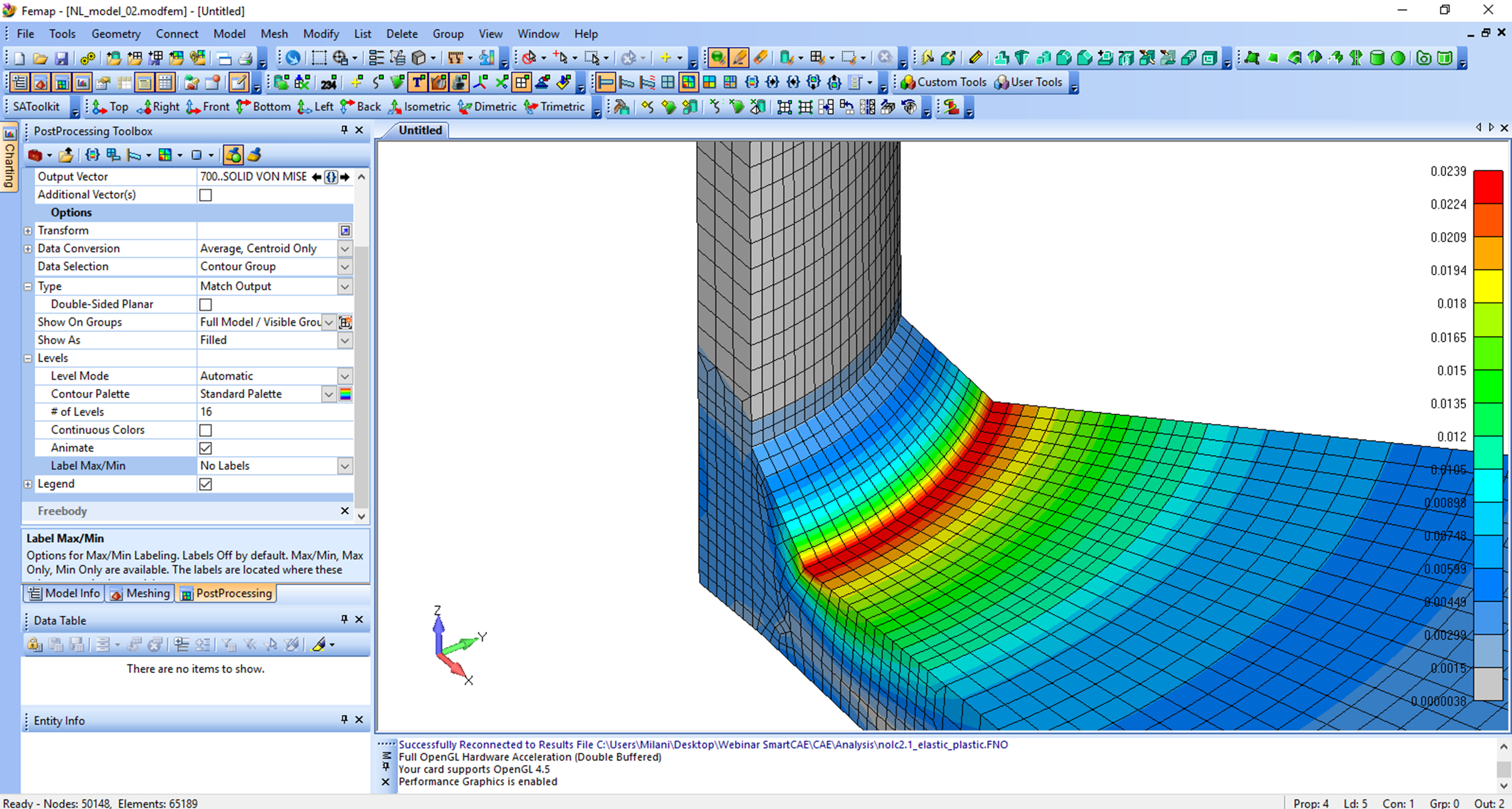
Figura 10 – Deformazione Equivalente Elasto-Plastica
Per la verifica a collasso plastico locale, occorre verificare che la deformazione plastica equivalente risulti inferiore alla deformazione limite ϵL, termine che dipende sia dal materiale che dallo stato tensionale in corrispondenza della zona sotto analisi.
I termini che legano la deformazione limite con lo stato tensionale sono “I1”, cioè il primo invariante del tensore di Cauchy e la tensione equivalente secondo Von Mises.
Tali valori, possono essere ricavati direttamente dagli output prodotti dal calcolo FEM, durante la fase di post-processing.
Il risultato di questa post-elaborazione è riportato in Figura 11. Il valore calcolato risulta inferiore a quello limite, pertanto la struttura è verificata anche al collasso plastico locale.

Figura 11 – Verifica a Collasso Plastico Locale
Nella deformazione totale è presente il termine ecf , col quale si tiene conto dell’eventuale presenza di deformazioni plastiche residue legate a precedenti lavorazioni di deformazione plastica a freddo. Questo valore può essere omesso soltanto nel caso in cui il prodotto subisca dei trattamenti termici di distensione prima della messa in opera.
Nel caso di stati di tensione triassiali di compressione, il primo invariante principale dello stato di tensione (la somma degli autovalori) è negativo, e la deformazione triassiale limite aumenta in maniera esponenziale. Ciò trova riscontro nel fatto che uno stato di tensione triassiale di trazione presenta un limite al di sopra del quale si ha il cedimento del componente per frattura fragile, mentre uno stato di tensione triassiale di compressione non comporta tale tipologia di collasso.
Conclusioni
Questo lavoro ha permesso di mettere in evidenza alcuni limiti dell’approccio lineare nella verifica dei recipienti in pressione. Non di rado infatti la presenza di rilevanti carichi di progetto, combinati all’applicazione della procedura di linearizzazione delle sollecitazioni, determina una non accettabilità del design, con la conseguente necessità di modificare la geometria iniziale o ridurre i carichi di progetto per rientrare all’interno del range ammissibile.
Per contro l’approccio non lineare, benché risulti computazionalmente più oneroso rispetto al calcolo lineare, e richieda una maggiore attenzione per la verifica a collasso plastico, permette una verifica più immediata dell’integrità strutturale del recipiente in pressione.
Nel nostro caso di studio, il componente analizzato, che non risultava verificato in campo elastico utilizzando la procedura di linearizzazione, supera la verifica utilizzando l’approccio dell’analisi non-lineare.
Approfondimenti
- Webinar sulla verifica non lineare dei recipienti a pressione, organizzato in collaborazione con Ener Consulting.
- La linearizzazione degli stress per la verifica dei recipienti a pressione
- Progettazione di attrezzature a pressione: risultati immediati e affidabili grazie all’analisi non-lineare