Indice dei contenuti
Spulciando nel mio archivio, ho trovato un vecchio articolo che ho presentato al congresso SEA-MED 2004. Anche se sono passati tanti anni alcuni degli argomenti trattati sono sempre di attualità, per questo motivo ho deciso di adattarne i contenuti per questo post.
Introduzione
La progettazione odierna costringe gli ingegneri a pensare soluzioni innovative e realizzabili in tempi sempre più stretti. Questo è vero sia per il progettista nautico che convive con i problemi della produzione, sia per colui che affronta il tema della competizione. Per entrambi è necessario valutare l’impatto di numerose variabili progettuali, inseguendo la soluzione di miglior compromesso (produzione) o l’eccellenza assoluta (prestazione).
Con il termine CAE (Computer Aided Engineering) vengono indicati i metodi e le discipline dell’ingegneria che consentono l’analisi dei problemi ingnegneristici mediante l’uso del calcolatore elettronico.
Il metodo degli elementi finiti (FEM) è una procedura numerica per ottenere delle soluzioni accurate di molti problemi strutturali, in tempi rapidi e con sforzi ragionevoli.
Il FEM offre molti vantaggi importanti al progettista
- Possibilità di analizzare facilmente strutture complicate (travi, gusci, continuo solido), di forma irregolare, costituite da materiali diversi (omogenei e compositi) e con condizioni al contorno complesse.
- Tipicamente, un software FEM commerciale è in grado di risolvere un’ampia varietà di problemi strutturali: lineari e non-lineari, dinamici, instabilità elastica (buckling).
- Il FEM può essere abbinato ad un sistema CAD per la creazione della geometria del componente da analizzare.
- Riduce i costi di test e riprogettazione, riducendo quindi il tempo di sviluppo del prodotto.
- Consente l’identificazione di problemi strutturali e/o di produzione prima della realizzazione del prodotto.
Per questi e molti altri motivi il FEM si è affermato in numerosi settori dell’ingegneria, tra cui la nautica da diporto. Lo scopo di questo lavoro è quello di illustrare alcune applicazioni del FEM, convenzionali e non, al mondo della progettazione di imbarcazioni da diporto.
Verifica di strutture in composito
I materiali compositi si sono affermati nella nautica da diporto (e non) per numerosi vantaggi tecnologici, quali:
- favorevole rapporto peso/resistenza rispetto ad altri materiali
- possibilità di beneficiare della “direzionalità” delle fibre per ottimizzare le prestazioni strutturali dei componenti, sia globali che locali.
Oltre agli aspetti tecnici, esiste una serie di risvolti economici che non vengono analizzati in questa sede.
Il progettista che approccia l’analisi di strutture in composito, deve avere ben presente anche alcuni aspetti pratici legati al materiale utilizzato:
- Le proprietà dei materiali utilizzati (elasticità, resistenza) presentano un certo grado di aleatorietà e di incertezza che dipende da molti fattori, non ultimo il ciclo di produzione del componente.
- Le proprietà del laminato dipendono, come noto, dalla sequenza di laminazione e sono tipicamente ortotropiche.
- I laminati in materiale composito, a differenza di quelli isotropi, hanno vari meccanismi di danneggiamento: rottura della fibra o della matrice (a sua volta con carichi ammissibili diversi per trazione, compressione, e taglio), delaminazione, …
Questi effetti possono essere correttamente valutati e tenuti sotto controllo in fase di progettazione realizzando un modello FEM dettagliato della struttura nel quale è possibile definire la sequenza di laminazione corretta. Come risultato dell’analisi è possibile produrre quegli indici di danneggiamento (noti come Failure Index) che esprimono la criticità dello stato di sollecitazione. Esistono svariati indici di danneggiamento (Max Stress, Max Strain, Hoffmann, Tsai-Hill, Tsai-Wu, per citarne alcuni), ognuno con i suoi pro, i suoi contro e il suo campo di applicazione.
In figura 1 è illustrata distribuzione del danneggiamento su di un trancio di scafo di motoryacht in composito (fibra di vetro e aramidica, resina epossidica), sottoposto ad una pressione idrostatica sul fondo. Le zone di colore più scuro sono quelle maggiormente sollecitate.
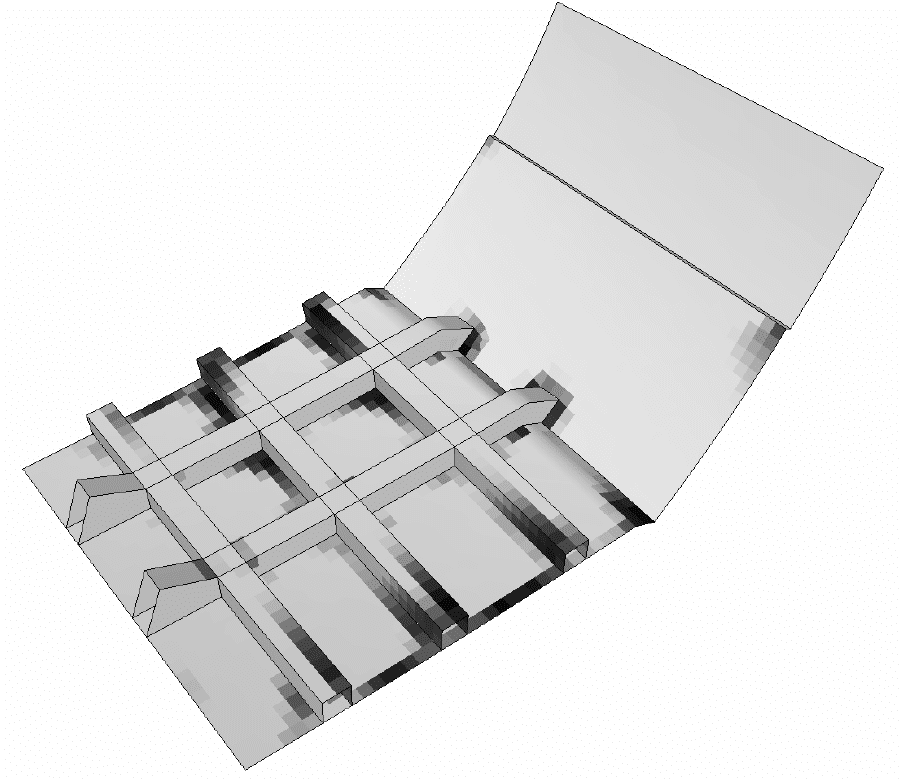
Fig. 1 – Distribuzione del Failure Index
Analisi statica con carichi inerziali
Uno dei problemi del calcolo FEM applicato alla nautica è quello dovere imporre al modello di analisi una condizione di vincolo “almeno isostatica”, per evitare labilità del sistema di equazioni. La condizione di labilità non è infatti accettata dal solutore FEM statico lineare.
La barca in navigazione, al contrario, non è soggetta a vincoli noti, ma si trova in una condizione di equilibrio dinamico istantaneo tra azioni molteplici: spinta di Archimede, spinta di propulsione, resistenza idrodinamica, inerzia.
Pertanto, qualsiasi sia il vincolo applicato all’imbarcazione, si tratta di una forzatura che, talvolta, può portare a risultati della simulazione “non fisici”, o perlomeno a mettere in discussione la validità delle ipotesi di analisi del modello.
Per aggirare questo limite, esiste una tecnica di simulazione FEM ormai consolidata da tempo nel settore aerospaziale, che prende il nome di Inertia Relief. Questa tecnica è correntemente utilizzata per simulare strutture in equilibrio dinamico, quali aerei e razzi in volo, satelliti in manovra.
Nella simulazione con Inertia Relief, l’analista seleziona un punto della struttura indicato come “supporto”. Il solutore FEM provvede quindi ad applicare alla struttura una distribuzione di accelerazioni uniformi tali che le forze di inerzia e i carichi di progetto (pressioni, forze) producano una reazione vincolare nulla sul supporto stesso (sistema di forze equilibrato).
Il metodo dell’Inertia Relief è stato utilizzato con successo per l’analisi e l’ottimizzazione dello scafo di un motoryacht.
Il modello (illustrato in figura 2) è stato realizzato discriminando le varie zone costitute da diverse laminazioni: chiglia, fondo, fianchi, madieri e longheroni. Ai fini dell’indagine sono state schematizzate anche tutte quelle parti non strutturali (paratie, rivestimenti, motori, serbatoi, masse distribuite) per tenerne debitamente in considerazione durante l’analisi di Inertia Relief.
Il carico è stato applicato utilizzando una distribuzione di pressione variabile lungo l’asse dello scafo, utilizzando i criteri forniti dal registro.
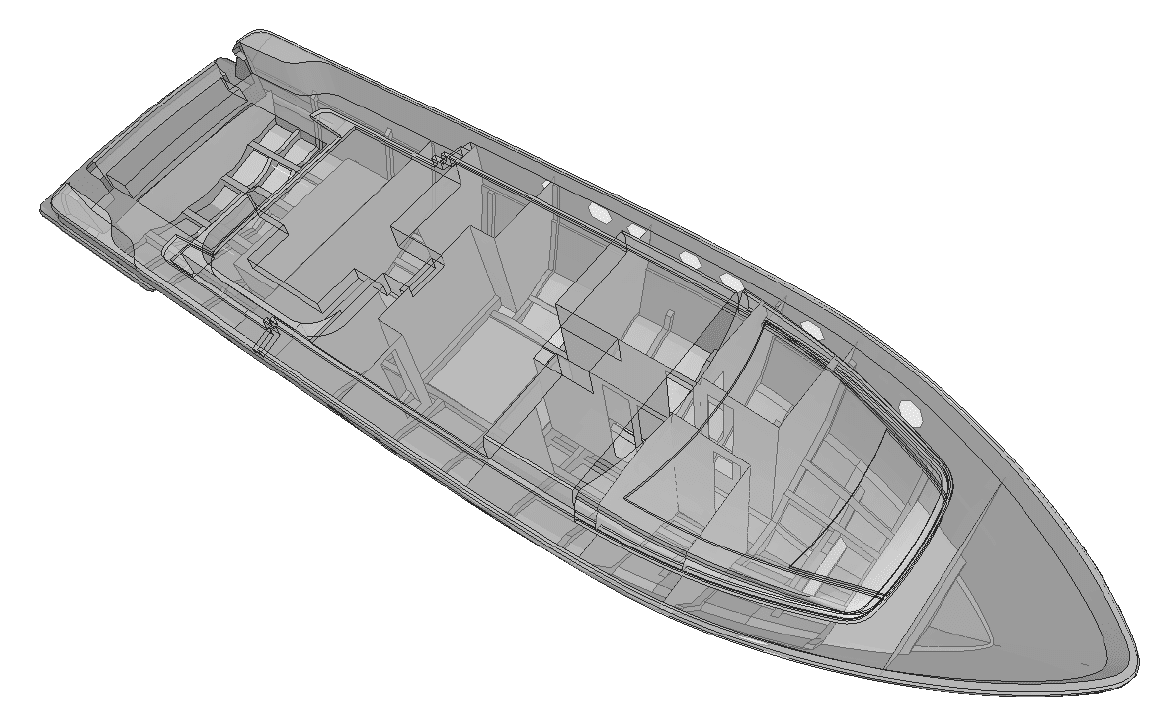
Fig. 2 – Modello FEM di motoryacht
In figura 3 è illustrata la deformata statica dell’imbarcazione, messa a confronto con la configurazione indeformata.
In figura 4 è illustrata la distribuzione di sollecitazione sulle parti strutturali. È possibile apprezzare l’elevato stato di sollecitazione di madieri e longheroni, mentre risulta poco sollecitata la carena.
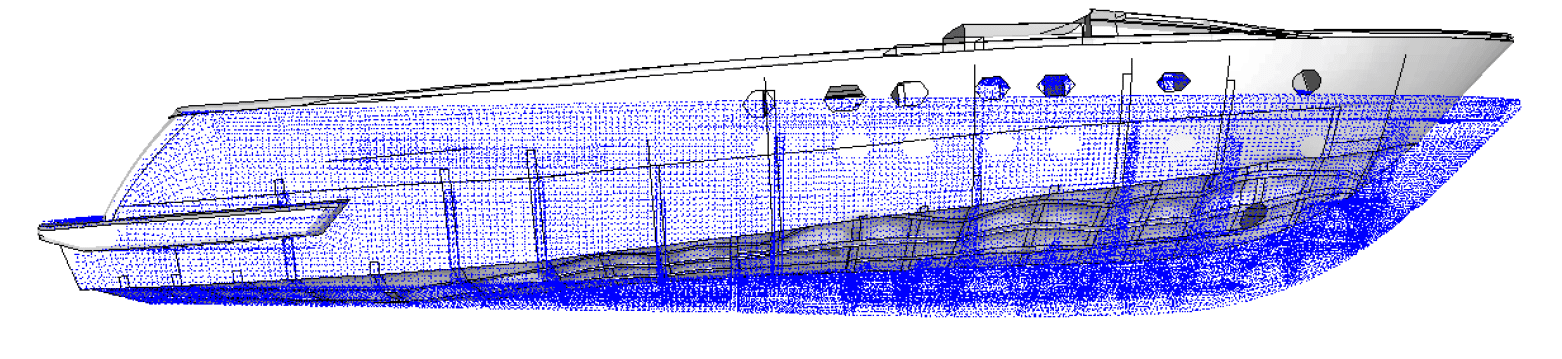
Fig. 3 – Deformata statica (amplificata)
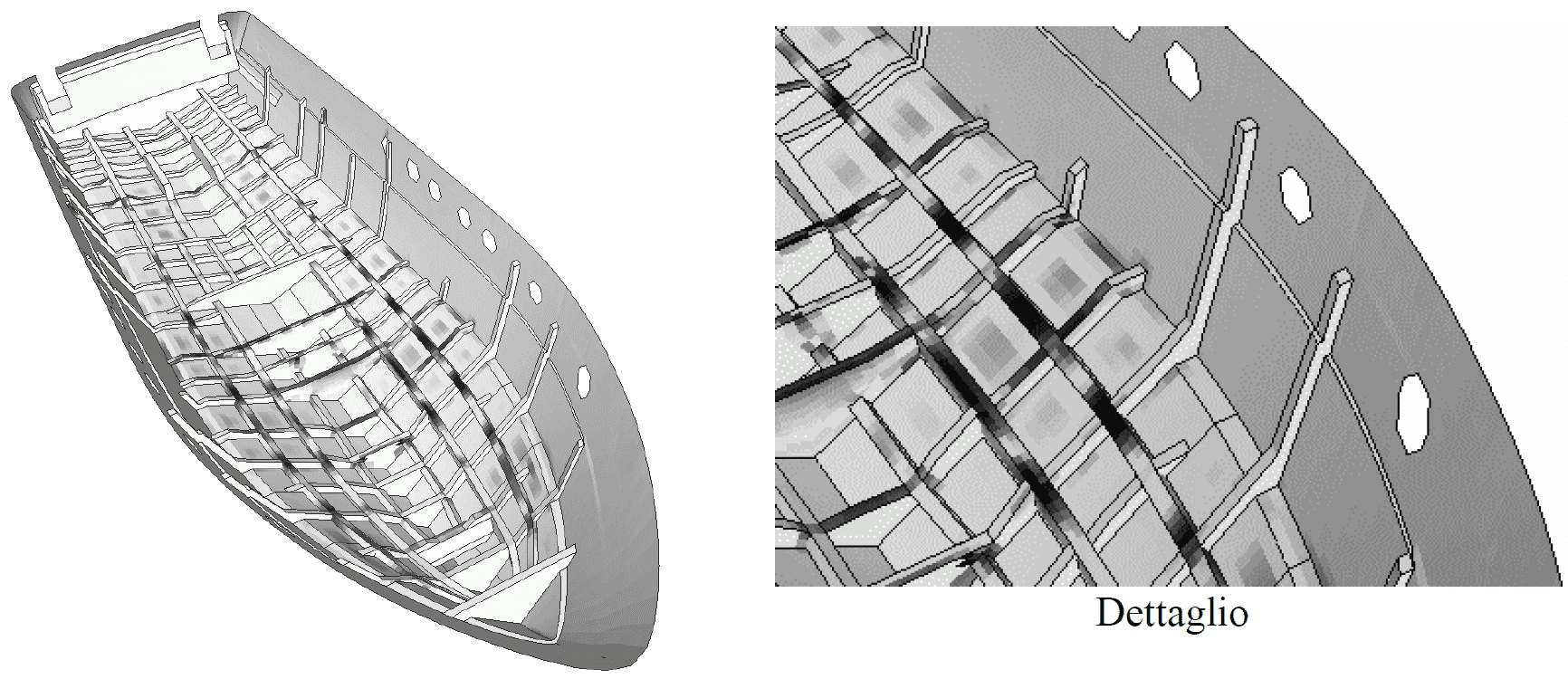
Fig. 4 – Distribuzione di stress sulle strutture interne e sullo scafo
Una volta messo a punto il modello di calcolo, è possibile utilizzarlo per ottimizzare la struttura dello scafo intero semplicemente variando la laminazione del modello FEM. Con poche ore di lavoro manuale è possibile quindi esplorare rapidamente ed economicamente un ampio spazio di progetto, identificando la struttura ottimale in base ai requisiti richiesti (leggerezza, rigidezza, costo, …).
Analisi di contatto tra corpi
Uno dei fenomeni fisici più comuni nella meccanica è quello del contatto tra i corpi. Contrariamente a quanto si possa pensare, si tratta di un problema frequente anche nella nautica e che si manifesta, ad esempio, tutte le volte in cui si voglia valutare la corretta distribuzione di carico tra due sistemi con collegamento flangiato. I casi più diffusi: il collegamento tra scafo e chiglia e quello tra chiglia e bulbo.
Purtroppo sia le normative, che i metodi di calcolo classici (es. teoria di Hertz) non forniscono uno strumento diretto per determinare la distribuzione della pressione di contatto su una flangia soggetta a carichi combinati (trazione/compressione, flessione, torsione), e le tensioni corrispondenti indotte sui componenti interessati.
Attraverso analisi FEM, per contro, è possibile simulare accuratamente fenomeni di contatto tra parti di geometria qualsiasi. In tal modo il progettista è sollevato dalla responsabilità di assunzioni semplificative “fantasiose” o dalla necessità di applicare sovradimensionamenti arbitrari.
A scopo esemplificativo, sono riportati due casi applicativi, cortesemente concessi da APM Keels.
Caso 1 – Chiglia sollevabile
Si tratta di un meccanismo nel quale la chiglia è collegata allo scafo mediante un perno, intorno al quale la stessa viene fatta ruotare tramite l’azione di attuatori idraulici.
La struttura della chiglia è realizzata mediante lamiere in acciaio elettrosaldate, con dei componenti in forte spessore nella zona di collegamento con il perno. La condizione di progetto è pari ad un carico di flessione laterale dato dalla rotazione della chiglia a 90° rispetto alla direzione verticale.
Lo scopo di questa analisi è stato quello di analizzare la corretta distribuzione di stress nella zona di collegamento tra chiglia e perno, per determinarne l’eventuale pericolosità e proporre, conseguentemente, delle modifiche progettuali.
Il modello della chiglia è realizzato mediante elementi guscio per le lamiere, elementi solidi per le boccole e il perno.
Le figure 5 e 6 illustrano la distribuzione di tensione data dal contatto, sul lato in trazione e quello in compressione della lama, mentre la figura 7 illustra una sezione del sistema chiglia-perno, evidenziando la distribuzione “fisica” delle tensioni.
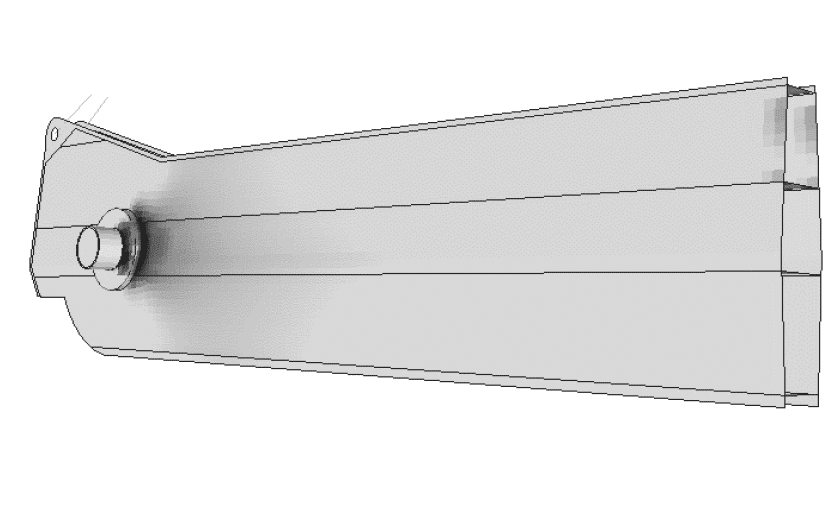
Fig. 5 – Tensione sul lato compresso
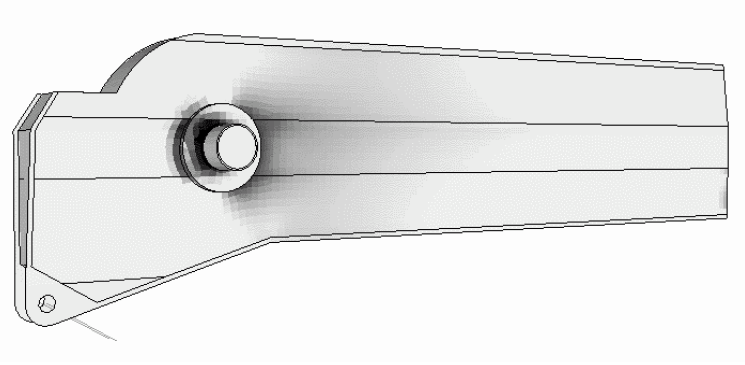
Fig. 6 – Tensione sul lato teso
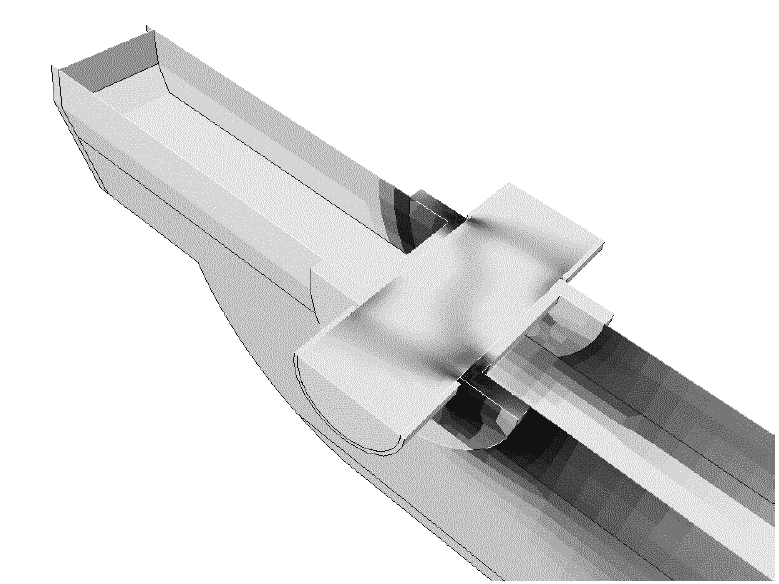
Fig. 7 – Sezione nella zona di collegamento
Caso 2 – Chiglia fissa
Questo è un altro caso molto comune: quello del collegamento del bulbo alla chiglia mediante flangia bullonata.
In questo caso la difficoltà è data dalla posizione molto arretrata del baricentro del bulbo, che tende a caricare in maniera non uniforme le viti della flangia. È stata determinata anche la distribuzione di stress all’interno dei cordoni di saldatura.
In figura 8 è illustrato il modello FEM della struttura. Anche in questo caso è stata effettuata una modellazione ibrida con elementi trave, piastra e solido.
La massa del bulbo è stata correttamente distribuita sul telaio, attraverso la modellazione del volume di piombo a elementi solidi tetraedrici (non mostrato in figura).
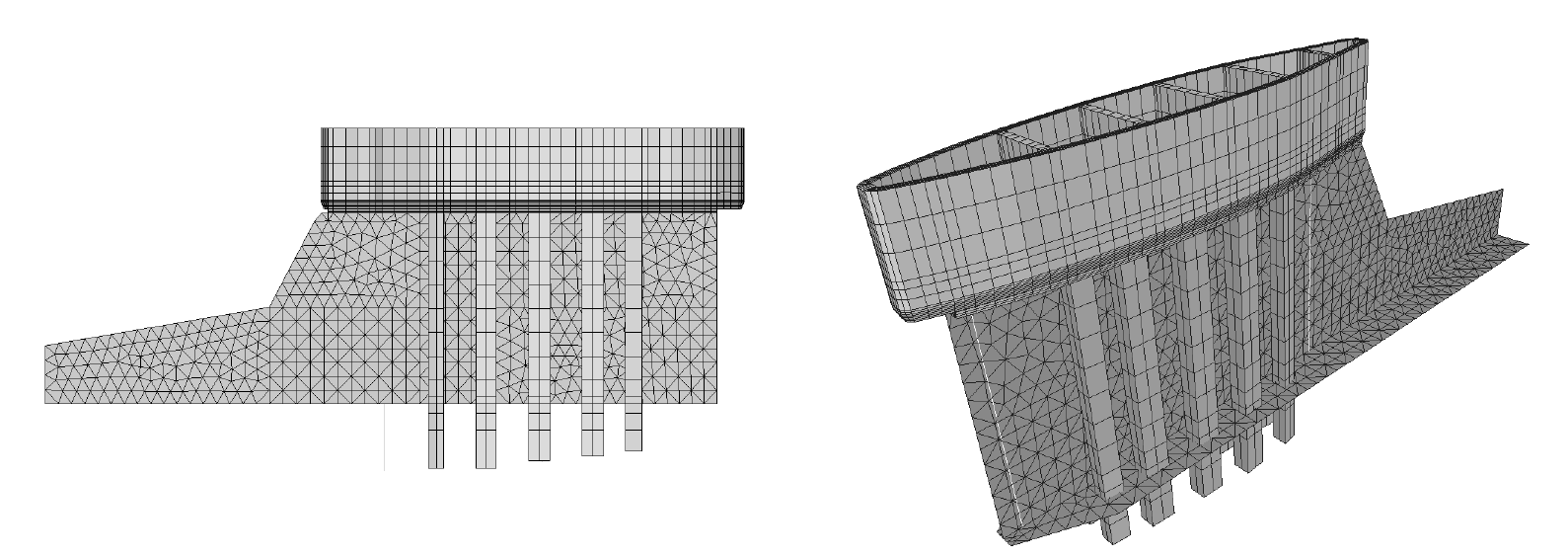
Fig. 8 – Modello FEM del collegamento bulbo-chiglia
In figura 9 è mostrato l’andamento dello stress di Von Mises sui lamierati della chiglia.
In figura 10 è evidenziata la distribuzione di stress all’interno dei cordoni di saldatura. Per entrambi i risultati è apprezzabile l’effetto della posizione del baricentro del bulbo, che tende scaricare buona parte del proprio peso sul bullone più arretrato.
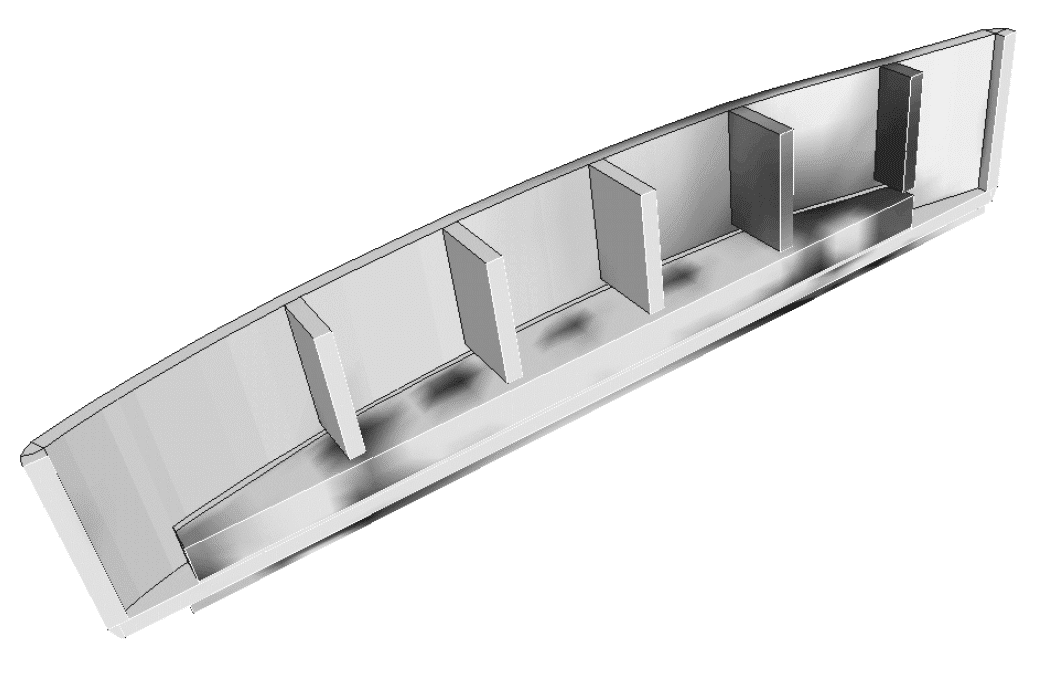
Fig. 9 – Tensione di Von Mises sulla chiglia
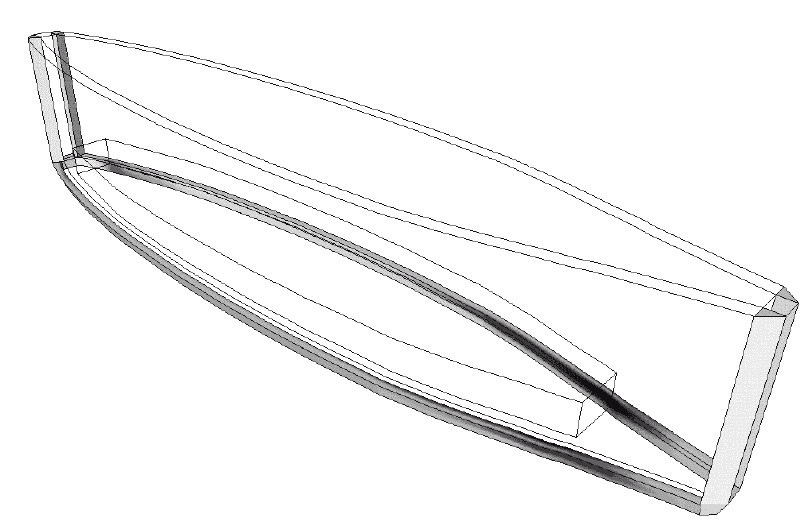
Fig. 10 – Tensione sui cordoni di saldatura
Conclusioni
Nel corso di questa breve trattazione, si sono potuti apprezzare i benefici apportati dall’analisi FEM nella progettazione di varie strutture e componenti nautici.
In particolare si è messo in evidenza come il FEM sia in grado di produrre i risultati strutturali cercati in tutti quei casi (e non sono pochi) nei quali le ipotesi per cui valgono i metodi di analisi classica non siano applicabili, fornendo al progettista quelle indicazioni con cui prendere serenamente e con cognizione di causa le proprie decisioni.
Nota
questo post è un estratto dell’articolo dal titolo “Metodi innovativi per l’analisi delle sollecitazioni e la verifica di strutture nautiche mediante FEM” presentato al convegno SEA-MED 2004.
Altri articoli sugli elementi finiti