Indice dei contenuti
Nell’ottimizzazione e progettazione dei materiali compositi laminati occorre utilizzare al meglio la simulazione al calcolatore. Al fine di riuscire a realizzare prodotti che abbiano le prestazioni desiderate ed allo stesso tempo siano economicamente sostenibili e semplici da realizzare.
La progettazione dei materiali compositi laminati
Nella progettazione dei manufatti in materiali compositi, il concetto di ottimizzazione è un tema obbligato per numerosi motivi.
Per prima cosa i materiali utilizzati hanno un elevato costo unitario. La tecnologia produttiva più utilizzata (la laminazione manuale con cura in autoclave) prevede tempi di produzione – e quindi costi – direttamente proporzionali alla quantità di materiale. Minimizzare tale quantità permette pertanto di contenere il costo del manufatto.
Molto spesso, il composito è utilizzato per applicazioni in cui ottenere il massimo la leggerezza del componente, rispettando requisiti di resistenza e rigidezza è fondamentale. Pertanto l’ottimizzazione del dimensionamento del laminato è obbligatoria.
Per questi motivi si fa largo uso del calcolo ad elementi finiti per generare progetti che siano contemporaneamente performanti ed economicamente sostenibili.
La tecnologia di produzione attuale dello hand-layup è un processo manuale che richiede un accurato studio di fattibilità affinché gli strati di composito siano effettivamente depositabili sullo stampo nei modi e con gli orientamenti di fibra di rinforzo desiderati in fase di dimensionamento.
Le sfide dell’ottimizzazione strutturale dei compositi laminati
Il composito offre una ampia libertà di progettazione.
La scelta del tipo di rinforzo (fibra di carbonio, vetro, kevlar etc., in forma di tessuto, unidirezionale, a gradi diversi di prestazioni e costi), spessore unitario delle pelli, l’orientamento delle fibre, la sequenza di laminazione rappresentano una ricca opportunità per ottenere le prestazioni meccaniche desiderate.
Proprio questo elevato numero di opzioni e variabili a disposizione costituisce una elevata complessità di gestione nell’ambito di una attività di ottimizzazione del design condotta con i tradizionali metodi ‘trial-and-error’ siano essi pure assistiti da simulazioni FEM.
Accade spesso che il componente in composito debba soddisfare molteplici requisiti di progetto, in termini di resistenza, rigidezza, peso, che tipicamente sono in conflitto tra di loro. La sfida risiede nel concepire una laminazione che permetta di centrare tutti gli obiettivi prestazionali prefissati nel rispetto dei vincoli di peso e costo.
Ad aggiungere un ulteriore – importante – livello di complessità alla tematica, si inserisce la necessità di rispettare i vincoli di producibilità, i più stringenti dei quali sono legati alla forma delle ply.
Il progetto ottimizzato deve tenere di conto anche di questi vincoli tecnologici per essere in ultima analisi realizzabile sia fattivamente che economicamente.
Ottimizzazione dei laminati: Manuale vs. Automatica
In generale, è possibile realizzare il disegno ottimizzato di una struttura in composito laminato spaziando da un approccio completamente manuale ad uno completamente automatico, passando per varie situazioni intermedie. Il workflow dei due approcci di ottimizzazione è illustrato in Figura 1 e sono evidenti le analogie.
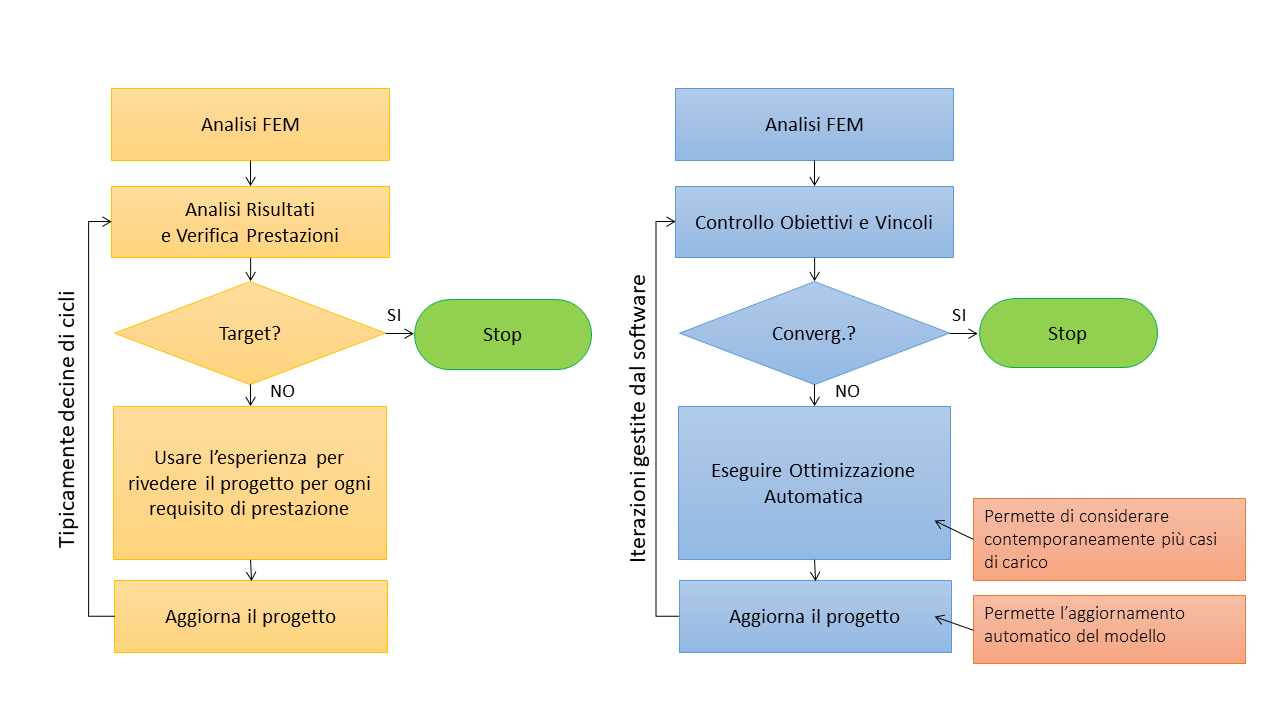
Figura 1 – Ottimizzazione Manuale e Automatica dei materiali compositi a confronto
Il punto di partenza di entrambi i metodi è il modello ad elementi finiti della struttura, nella quale è stata impostata una sequenza di laminazione di primo tentativo, che viene sottoposta alle condizioni di carico e vincolo. Nasce quindi un ciclo nel quale, a ogni iterazione, viene modificata la sequenza di laminazione sulla base dei risultati strutturali fino al raggiungimento del dimensionamento voluto.
La differenza sostanziale tra questi due approcci è che nel caso dell’ottimizzazione manuale, risulta fondamentale l’esperienza e l’intuizione dell’analista per guidare il progetto iterazione dopo iterazione. Essendo un processo manuale il tempo richiesto per ogni iterazione è elevato, questo limita di fatto il numero di iterazioni realmente studiabili prima di raggiungere il disegno ottimale.
Nel caso invece dell’ottimizzazione automatica, storicamente il principale limite della tecnologia numerica era la mancanza nel software di una forma di “esperienza” che fosse in grado di generare sequenze di laminazione non solo performanti, ma anche relativamente semplici da realizzare in produzione.
I vari approcci all’ottimizzazione dei compositi laminati
Negli anni, all’interno dei software ad elementi finiti, sono stati implementati svariati algoritmi per aiutare il progettista a definire una sequenza di laminazione ottimizzata in grado di rispettare
Ottimizzazione Parametrica
E’ l’approccio disponibile ad esempio nella SOL 200 di Simcenter Nastran. In questo approccio l’analista definisce a priori la forma delle pelli attraverso le schede PCOMP. Pertanto la forma rimane invariata durante il ciclo di ottimizzazione. I parametri che diventano oggetto di studio risultano; ad esempio spessori delle pelli, direzione delle fibre, moduli di elasticità dei materiali. Un esempio di Ottimizzazione Parametrica è mostrato in Figura 2.
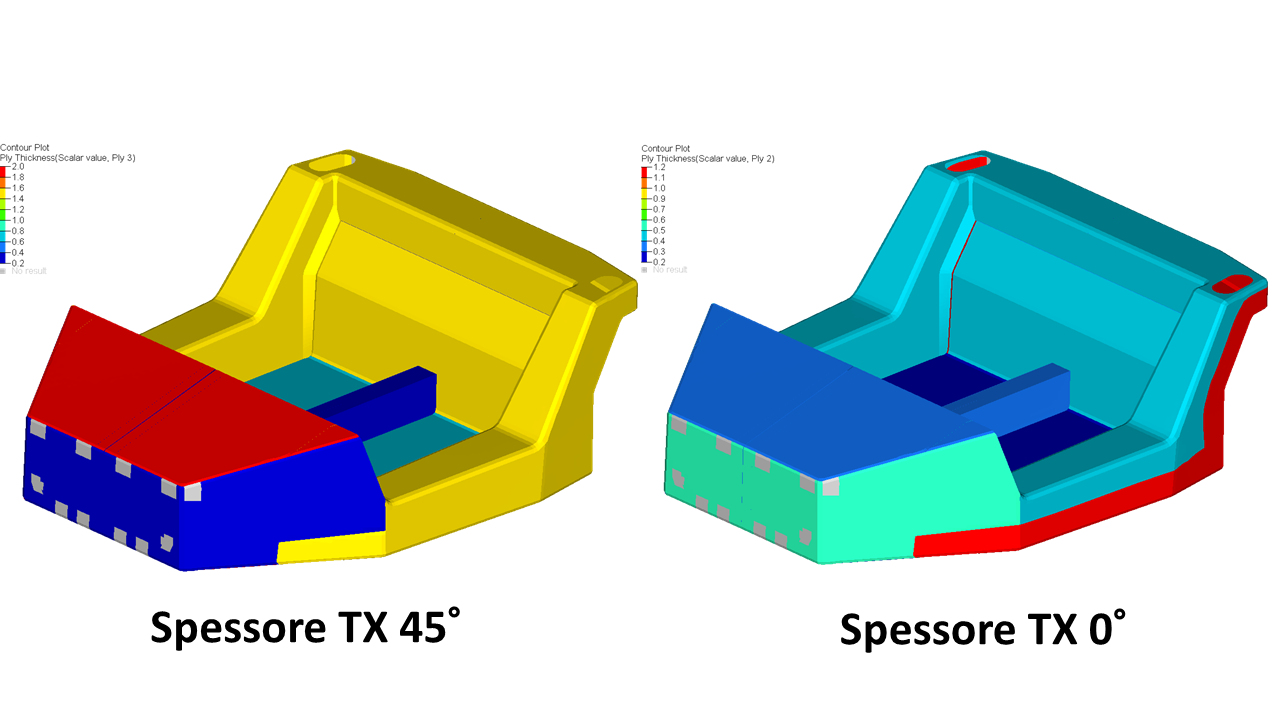
Figura 2 – Esempio di Ottimizzazione Parametrica
Ottimizzazione Topologica Freesize
Questo approccio è simile all’Ottimizzazione Parametrica ma con l’individuazione della distribuzione continua di spessore locale. Il punto di partenza di questo studio è l’ottimizzazione topologica. Un esempio di ottimizzazione Topologica Freesize è mostrato in Figura 3.
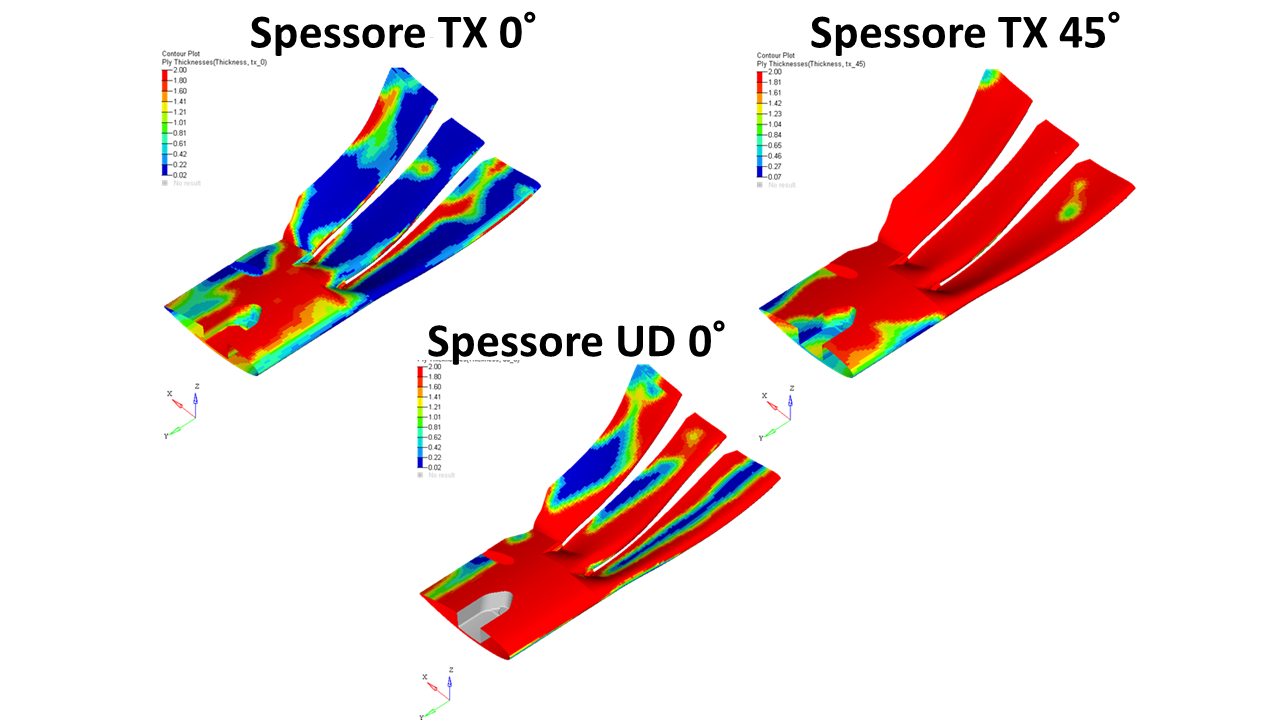
Figura 3 – Esempio di Ottimizzazione Topologica Freesize
Ottimizzazione Topologica Size
Questo metodo è un passaggio successivo all’ottimizzazione Freesize, dalla quale si deriva la forma delle plies candidate. La Topologica Size offre la possibilità di definire alcuni criteri per vincolare gli spessori di ply (es. valori discreti) e del laminato. Un esempio di ottimizzazione Topologica Size è mostrato in Figura 4.
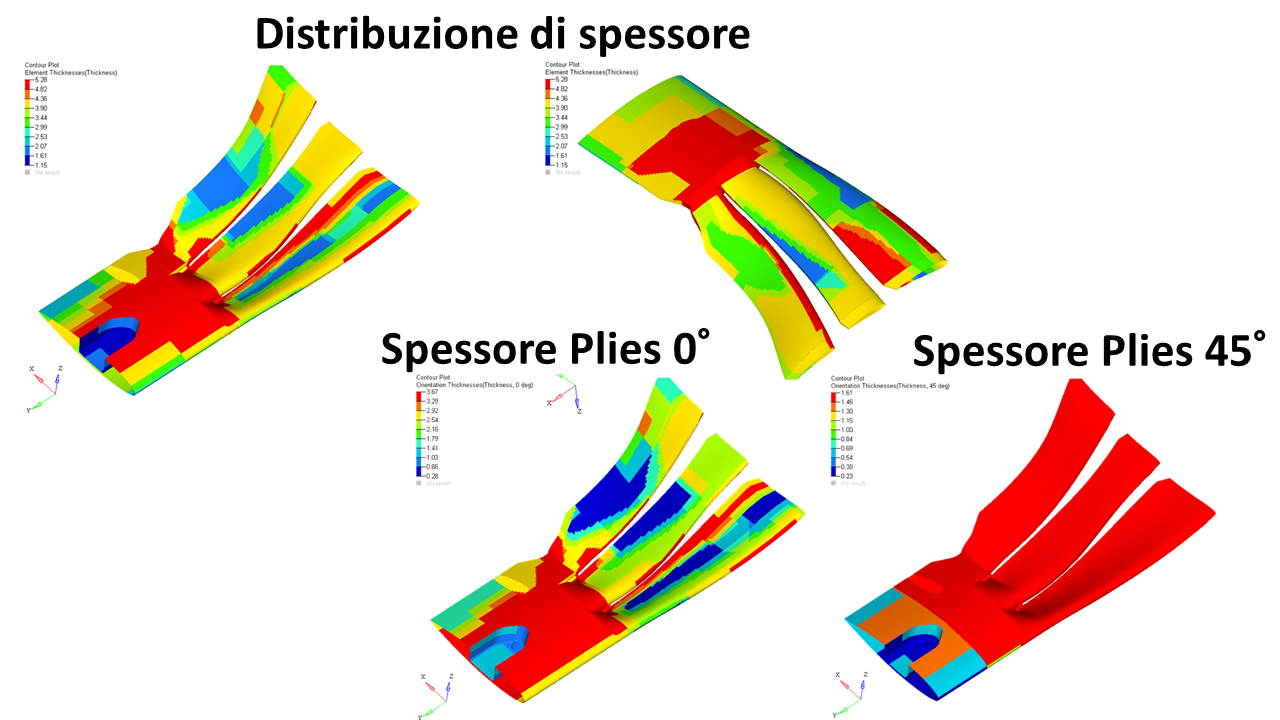
Figura 4 – Esempio di Ottimizzazione Topologica Size
Ottimizzazione Ply-Based
L’Ottimizzazione Ply-Based è un approccio che combina aspetti delle tecniche precedenti: controllo manuale, possibilità di ottimizzare parametricamente e individuare le forme delle pelli in modo più o meno vincolato dall’utente. Un esempio di Ottimizzazione Ply-Based è mostrato in Figura 5.
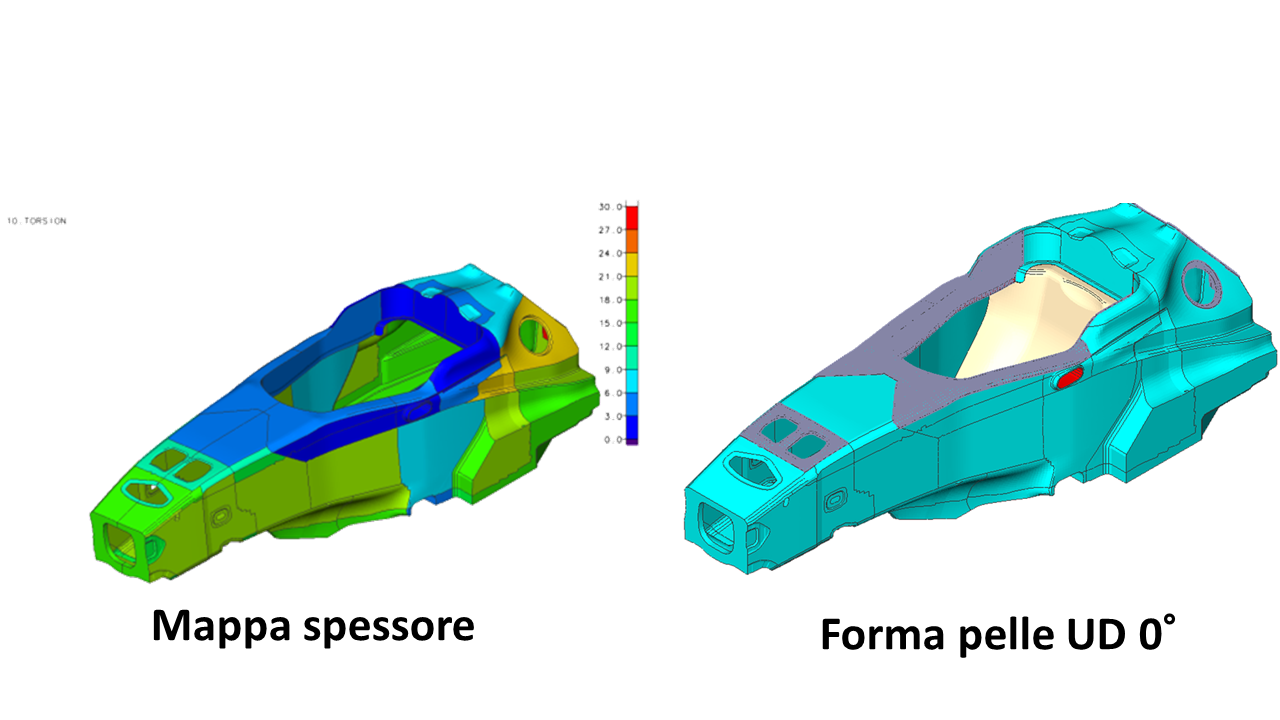
Figura 5 – Esempio di Ottimizzazione Ply-Based
Questa tecnologia è la base del software OptiAssist sviluppato da GRM Consulting. OptiAssist è un’interfaccia utente che è in grado di aiutare l’analista FEM a impostare i propri studi di ottimizzazione strutturale dei laminati per pilotare i solutori Genesis e la SOL 200 di Simcenter Nastran.
Il workflow di ottimizzazione con OptiAssist
L’ottimizzazione di un laminato con OptiAssist è un processo in tre fasi principali.
Generazione del laminato candidato
Per prima cosa si importa o si crea un laminato base, costituito da pelli ‘candidate’ all’ottimizzazione, sulla mesh ad elementi finiti che costituisce il punto di partenza dello studio di ottimizzazione. Questa fase può essere realizzata utilizzando sia l’interfaccia di OptiAssist stesso, oppure importando dall’esterno il laminato in formato PCOMPG, ad esempio utilizzando modellatori dedicati ai compositi come Laminate Tools, Fibersim o Catia CPD, ma anche modellatori FEM tradizionali come Hypermesh, ANSA, Femap, Simcenter etc..
Ottimizzazione strutturale
Una volta definita il laminato candidato, è possibile eseguire l’ottimizzazione del numero e della forma (‘topometry’) delle pelli di composito adottando due diverse strategie.
Ottimizzazione Automatica: Approccio “Grid Edge Length Topometry”.
Con questo approccio OptiAssist è in grado di generare autonomamente il profilo del contorno delle pelli, sulla base di una logica di definizione dei profili che segue una griglia X, Y, Z predefinita e pertanto producendo forme di pelli che derivano dalla combinazione di ‘patch’ di elementi della griglia stessa, come esemplificato in Figura 6.
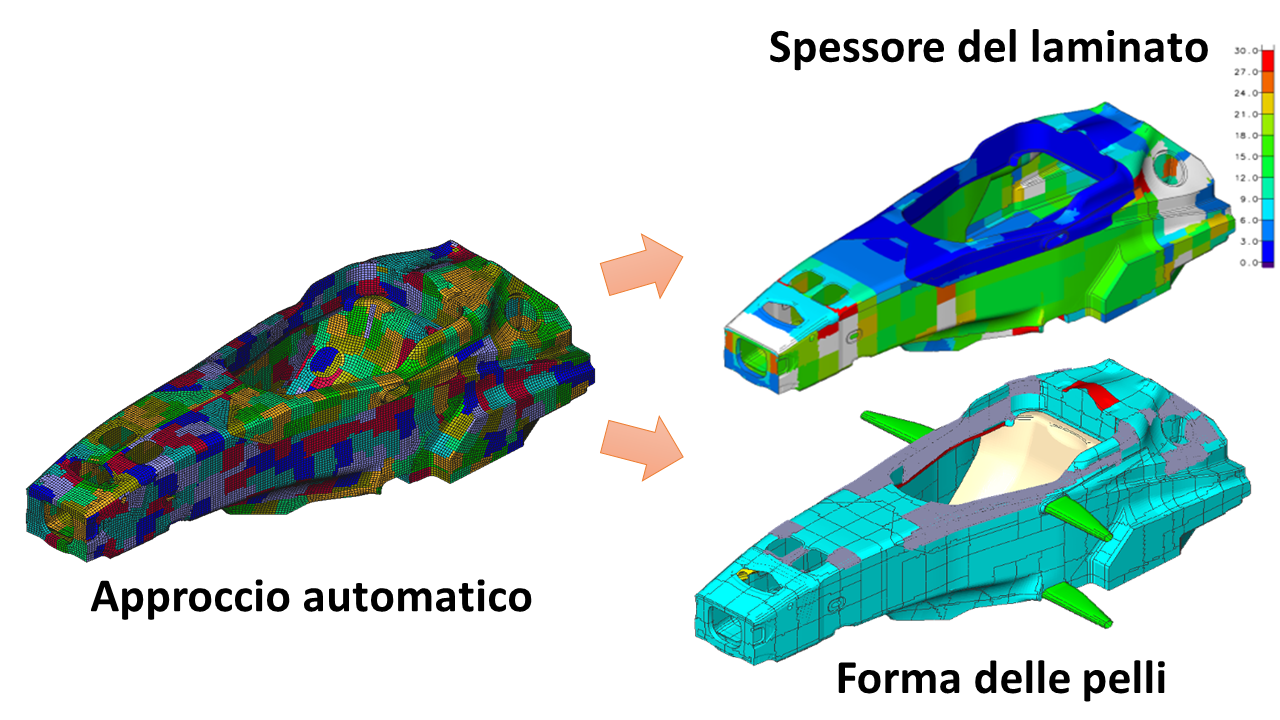
Figura 6 – Ottimizzazione Topometrica con OptiAssist
Ottimizzazione Semi-Automatica: Approccio “User Defined Topometry”.
Ciò che differenzia OptiAssit dagli altri software di ottimizzazione strutturale per compositi è la possibilità di utilizzare un approccio semi-automatico, definendo gli User Pattern, ovvero imponendo al modello il rispetto di determinate patch geometriche al fine di mantenere il controllo sul processo produttivo e avere un diretto trasferimento alla produzione del disegno ottimizzato (Figura 7).
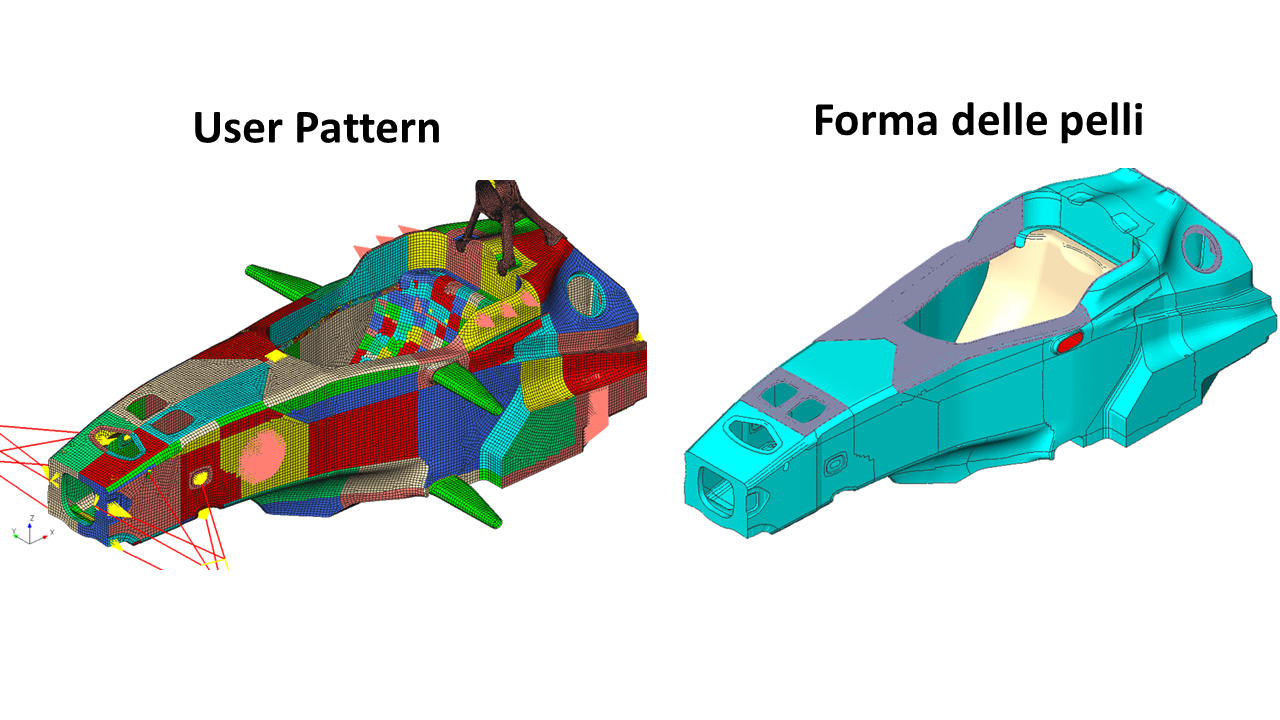
Figura 7 – Ripartizione del modello con gli User Pattern
Gli approcci sopra elencati possono anche essere combinati tra loro. Ad essi tipicamente si sovrappone l’ottimizzazione parametrica del numero di strati e dell’orientamento delle fibre, in modo da pervenire alla definizione completa della sequenza di laminazione. E’ possibile imporre all’ottimizzatore di rispettare vincoli di simmetria del laminato, di spessore totale, locale, massimo numero di strati consecutivi di un dato materiale etc..
Esportazione del layup ottimizzato
E’ questa una fase estremamente critica in quanto permette di trasmettere al reparto produzione le informazioni – altamente complesse – prodotte dall’ottimizzazione strutturale. Tipicamente questa fase rappresenta on collo di bottiglia in un processo di ottimizzazione FEM, dovuto alla complessità intrinseca delle informazioni stesse e alla necessità di convertirle in un formato (grafico, CAD, …) utilizzabile in fase di produzione del manufatto.
Con OptiAssist, una volta completato il ciclo di ottimizzazione è possibile esportare le informazioni contenute nel modello FEM per generare i dati di produzione del laminato: costruzione del PlyBook in formato Powerpoint, esportazione del file .layup verso Laminate Tools, Fibersim e Catia CPD, esportazione della forma 3D delle pelli come STL o IGES.
Caso di studio: INEOS Team UK
Il software OptiAssist per Simcenter 3D è stato utilizzato da INEOS Team UK per lo sviluppo della imbarcazione di classe America’s Cup che ha partecipato alle recenti competizioni in Nuova Zelanda. OptiAssist è stato utilizzato a vari livelli di dettaglio nell’ottimizzazione delle strutture principali e dei componenti dell’imbarcazione realizzati in fibra di carbonio.
- Globale
- Sotto-Assieme
- Componente
Ottimizzazione a livello Globale: rigidezza dello scafo
Al fine di ottenere le massime prestazioni aerodinamiche e idrodinamiche, occorre che le forme delle superfici bagnate siano più fedeli possibili a quelle analizzate con i software di fluidodinamica.
L’entità delle forze che passano per il piede d’albero, dal boma, dagli attacchi degli stralli, della chiglia e dei foil, introducono delle deformazioni che devono essere limitate per mantenere la geometria desiderata. Non è possibile irrigidire a proprio piacimento in quanto aggiungere materiale vuol dire aggiungere massa e quindi peggiorare le prestazioni della barca.
Pertanto questo studio è stato impostato come un’ottimizzazione per minimizzare la massa, imponendo la deflessione massima nei punti di attacco degli stralli allo scafo. Oggetto dell’ottimizzazione, ovviamente, è la laminazione dello scafo.
In Figura 8 si vedono alcuni risultati del processo di ottimizzazione; in particolare sono riportate le distribuzioni dei rinforzi di unidirezionale posizionati lungo la carena e la coperta. Da queste immagini si apprezza la scalatura progressiva del rinforzo. Questa è una capacità al momento unica di OptiAssist che permette di generare laminazioni facilmente interpretabili ed effettivamente realizzabili.
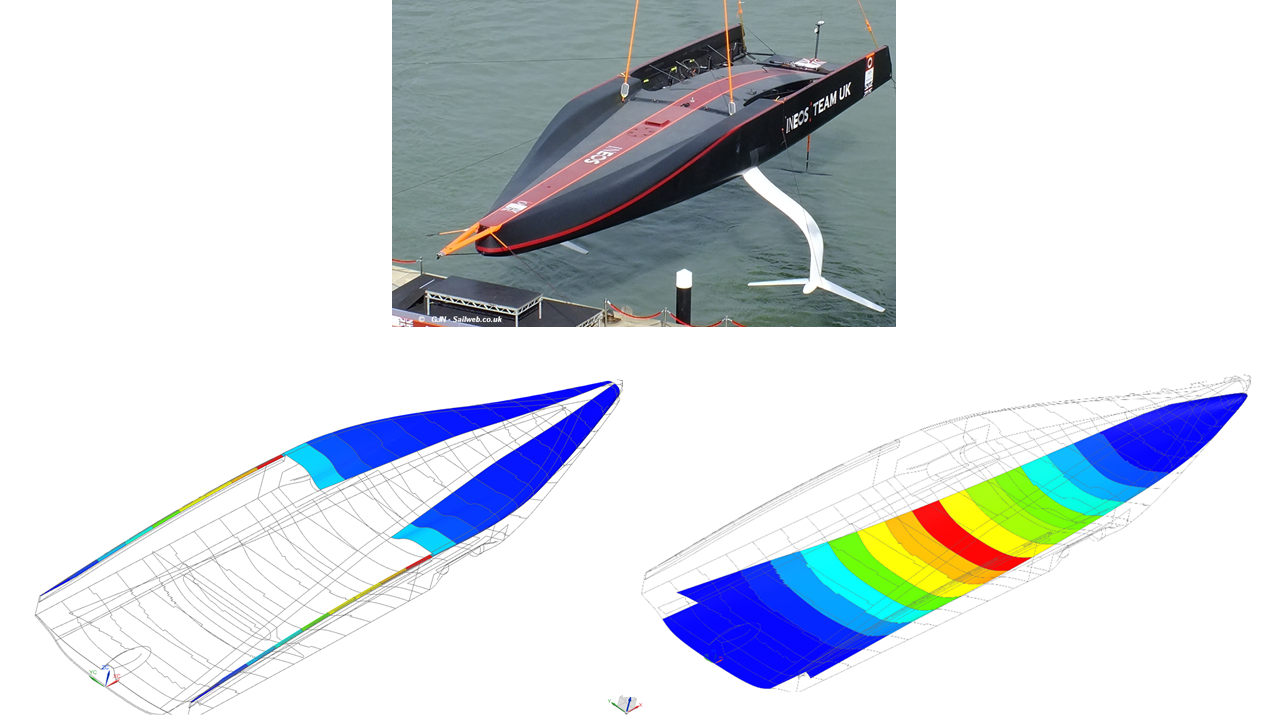
Figura 8 – Scalatura delle pelli nella carena e nella coperta
Ottimizzazione a livello di Sotto-Assieme: paratia del piede d’albero
La paratia del piede d’albero è la struttura primaria che viene posizionata sotto l’albero e si può dire che una barca a vela venga costruita intorno a essa. Di fatto tutte le forze generate dalle vele ed equilibrate dalla chiglia o dai foil passano per questo nodo strutturale:
- Il carico del vento sulle vele determina una flessione dell’albero, ostacolata dagli stralli a poppa, prua e nella sezione del piede.
- I carichi di trazione sugli stralli sono equilibrati da uno stato di compressione sull’albero.
- Questi carichi determinano un momento ribaltante sulla barca che viene riequilibrato da un momento raddrizzante prodotto dalla chiglia (nelle imbarcazioni tradizionali) oppure dall’hydrofoil.
Tutte queste forze convergono alla paratia del piede dell’albero, che pertanto risulta molto sollecitata. A livello di ottimizzazione, sono stati definiti tre scenari di carico con obiettivi differenti in termini di rigidezza e resistenza.
In Figura 9 vengono illustrati i vari User Pattern della struttura nominale utilizzati da OptiAssist per l’ottimizzazione strutturale. In Figura 10 viene mostrata la distribuzione di spessore del disegno ottimizzato. OptiAssist è stato in grado di generare dei rinforzi scalati sia per quanto riguarda i nastri di rinforzo unidirezionale che per le zone con il tessuto, in grado di soddisfare i requisiti di resistenza e rigidezza, minimizzando il peso complessivo della struttura.
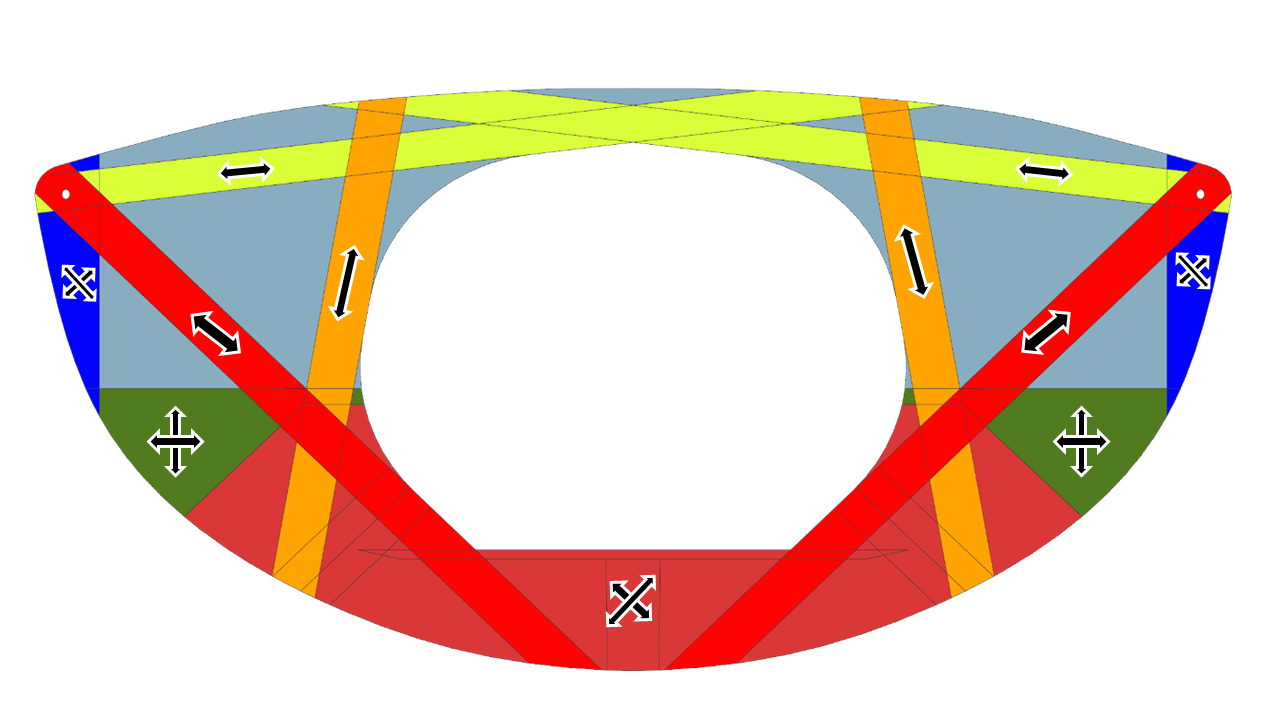
Figura 9 – Definizione degli User Pattern di tessuto e unidirezionale
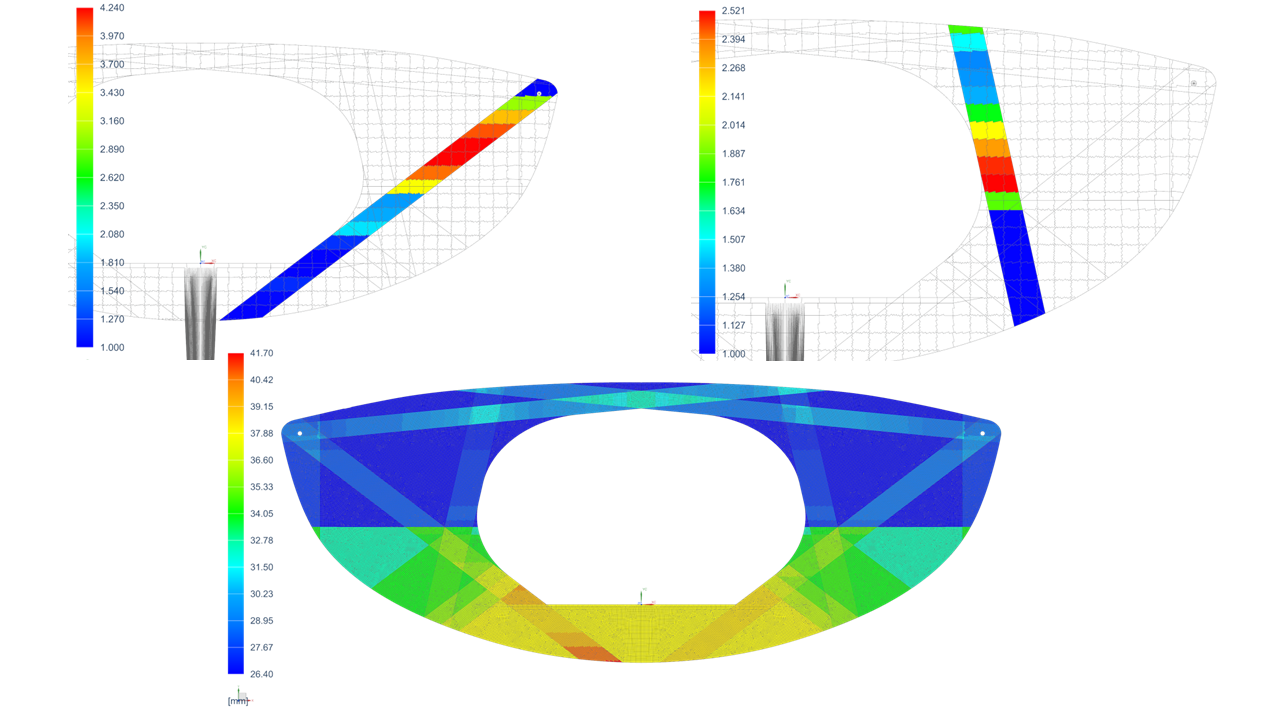
Figura 10 – Scalatura delle pelli nella paratia del piede d’albero
Ottimizzazione a livello di Componente: staffe della trasmissione
Il terzo oggetto su cui vediamo l’applicazione di OptiAssist è la struttura su cui vengono montate le trasmissioni per le macchine ad azionamento manuale (argani, pompe). L’obiettivo dell’ottimizzazione è quello di minimizzare la massa delle staffe sotto l’azione di 4 storie di carico differenti, rispettando i requisiti di resistenza e rigidezza.
Nella Figura 11 si vede l’andamento della funzione obiettivo tra le varie iterazioni, in questo caso la massa della staffa. Partendo dal disegno iniziale che era fuori obiettivo come rigidezza e resistenza, l’ottimizzatore ha prima aumentato gli spessori per rientrare nei vincoli di rigidezza e resistenza desiderati, per poi andare a perfezionare la distribuzione di spessore per rimuovere il materiale dove non è necessario.

Figura 11 – Ottimizzazione degli spessori dei supporti
Conclusioni
Riassumendo, quali sono i benefici che OptiAssist garantisce a chi si occupa della progettazione delle parti in composito?
Alte prestazioni strutturali in scenari complessi
Per prima cosa, OptiAssist possiede una tecnologia unica per gestire sia gli aspetti di ottimizzazione strutturale multi-obiettivo in termini di configurazioni di carico e obiettivi di massa, rigidezza, resistenza. Questo permette di ottenere il massimo delle prestazioni strutturali dal proprio progetto.
Concetti di laminazione innovativi
Il secondo aspetto fondamentale è quello dell’innovazione. Lasciando la massima libertà all’ottimizzatore, OptiAssist può fornire delle idee concettuali molto interessanti che possono aiutare il progettista a individuare rapidamente le zone da rinforzare e a definire la strategia di laminazione migliore.
Producibilità del laminato
Queste idee concettuali, grazie all’utilizzo della topometria definita dall’utente, possono poi essere tradotte agevolmente in una sequenza di laminazione davvero realizzabile, minimizzando il numero di pelli e razionalizzando l’uso del materiale. Questo vuol dire non solo ottenere il massimo delle prestazioni, ma essere sicuro che la sequenza di laminazione passerà il vaglio della produzione.
Accorciamento dei tempi di sviluppo
Ultimo ma non ultimo, se ragioniamo in termini di tempi di sviluppo, il confronto tra l’approccio tradizionale manuale, basato sull’esperienza dell’analista e quello semi-automatico basato sull’ottimizzazione Ply-Based è nettamente a favore di quest’ultimo.
Con OptiAssist e l’ottimizzazione Ply-Based potete concepire sequenze di laminazione più performanti, utilizzando meno materiale e impiegando molto meno tempo rispetto all’approccio tradizione.
Cosa è OptiAssist
OptiAssist è un software sviluppato da GRM Consulting che offre una famiglia di strumenti completi per l’analisi FEA, lo sviluppo del laminato e una suite di funzioni per la creazione di report di produzione per gli ingegneri che progettano manufatti in composito. Attraverso l’interfaccia di OptiAssist, gli ingegneri sono in grado di sviluppare in modo efficiente i progetti dei compositi laminati. Lavorando attraverso le seguenti fasi chiave: modellazione del laminato, ottimizzazione delle forme delle pelli, comunicazione dei dati del laminato a chi si occupa della produzione. OptiAssist è compatibile con i principali ambienti di modellazione FEM e con gli strumenti di gestione dei laminati come Laminate Tools, Fibersim e Catia CPD. OptiAssist è distributo in Italia da SmartCAE. Per maggiori informazioni: https://optiassist.smartcae.com/
Argomenti correlati
Webinar
- Ottimizzare le strutture in composito con OptiAssist per Genesis
- Introduzione a OptiAssist per Simcenter 3D
Articoli